Rolling process beneficial to spheroidizing annealing of Cr and Mo steel
A process and annealing technology, applied in the field of metallurgy, can solve undisclosed problems
- Summary
- Abstract
- Description
- Claims
- Application Information
AI Technical Summary
Problems solved by technology
Method used
Image
Examples
Embodiment 1
[0026] A steel plant adopts 325mm×280mm bloom continuous casting-blooming-wire rolling process to produce Φ13mm wire rod for high-strength bolts. The steel grade and composition are shown in Table 1.
[0027] Table 1 Grades and compositions of steel grades
[0028] Grade C Si mn P S Cr Mo SCM435 0.35 0.2 0.65 0.013 0.007 0.95 0.2
[0029] (1) Open the billet after continuous casting. During the billet opening process, the heating temperature is 1100°C and the heating time is 7 hours;
[0030] (2) Roll the steel billet after billeting. During the rolling process, the rolling temperature is 1050°C, the final rolling temperature is 875°C, and the spinning temperature is 800°C; hold at 850°C for 1 hour, and corrode after quenching to obtain Austenite The comparison of bulk grains such as image 3 As shown, it can be seen from the figure that image 3 (b) The medium austenite particles are more refined and homogeneous;
[0031] (3) After roll...
Embodiment 2
[0036] A steel plant adopts the 325mm×280mm bloom continuous casting-blooming-wire rolling process to produce Φ10mm wire rod for high-strength bolts. The steel grade and composition are shown in Table 1.
[0037] (1) Open the billet after continuous casting. During the billet opening process, the heating temperature is 1130°C and the heating time is 5 hours;
[0038] (2) Roll the steel billet after billeting. During the rolling process, the rolling temperature is 1080°C, the final rolling temperature is 895°C, and the spinning temperature is 815°C; hold at 850°C for 1 hour, and corrode after quenching to obtain Austenite The comparison of bulk grains such as Figure 5 As shown, it can be seen from the figure that Figure 5 (b) The medium austenite particles are more refined and homogeneous;
[0039](3) After the steel billet is rolled, it is rapidly cooled to 600°C at a cooling rate of 10°C / s, and then kept warm on the roller table cooling line until about 300°C, and the rol...
Embodiment 3
[0045] A steel plant adopts the 325mm×280mm bloom continuous casting-billet opening-wire rolling process to produce Φ8mm wire rod for high-strength bolts. The steel grade and composition are shown in Table 1.
[0046] (1) Open the billet after continuous casting. During the billet opening process, the heating temperature is 1110°C and the heating time is 6 hours;
[0047] (2) Roll the steel billet after billeting. During the rolling process, the rolling temperature is 1070°C, the final rolling temperature is 885°C, and the spinning temperature is 810°C; hold at 850°C for 1 hour, and corrode after quenching to obtain Austenite The comparison of bulk grains such as Figure 7 As shown, it can be seen from the figure that Figure 7 (b) The medium austenite particles are more refined and homogeneous;
[0048] (3) After the steel billet is rolled, it is rapidly cooled to 570°C at a cooling rate of 15°C / s, and then kept warm on the roller table cooling line until about 330°C, and t...
PUM
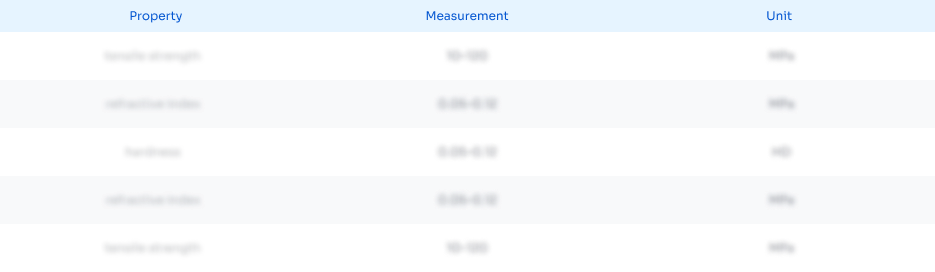
Abstract
Description
Claims
Application Information

- Generate Ideas
- Intellectual Property
- Life Sciences
- Materials
- Tech Scout
- Unparalleled Data Quality
- Higher Quality Content
- 60% Fewer Hallucinations
Browse by: Latest US Patents, China's latest patents, Technical Efficacy Thesaurus, Application Domain, Technology Topic, Popular Technical Reports.
© 2025 PatSnap. All rights reserved.Legal|Privacy policy|Modern Slavery Act Transparency Statement|Sitemap|About US| Contact US: help@patsnap.com