Method for preparing aerated concrete by utilizing lead zinc tailings
An air-entrained concrete and lead-zinc technology is applied in the field of preparing new porous thermal insulation building wall materials, which can solve the problems of low quartz content, and achieve the effects of reducing the settling speed, improving the pore structure and reducing the density.
- Summary
- Abstract
- Description
- Claims
- Application Information
AI Technical Summary
Problems solved by technology
Method used
Image
Examples
Embodiment 1
[0036] Example 1: Combining image 3 , See Table 3 for the mixture ratio.
[0037] Table 3 Embodiment 1 Mixture ratio
[0038]
[0039] Step 1: Add 25 kg of water, 4.35 kg of 4wt% PVA solution, 15 kg of quartz sand powder, 5 kg of diatomaceous earth, 15 kg of lead-zinc tailings (1), 1.5 kg of gypsum and 5.5 kg of cement in sequence Stir in the bucket for 5min;
[0040] Step 2: After adding 0.1 kg of polycarboxylate superplasticizer, add 19 kg of lime and stir for 5 minutes;
[0041] Step 3: Add a mixed solution of 0.08 kg of aluminum powder and 0.025 kg of foam stabilizer sodium dodecylbenzene sulfonate into the slurry and stir for 3 minutes;
[0042] Step 4: Pour the slurry into the mold;
[0043] Step 5: Put the mold into a thermal curing kiln at 50°C for static maintenance;
[0044] Step 6: After 3-5 hours of static maintenance, demould, and cut the aerated concrete body;
[0045] Step 7: After cutting, continue to put it into the thermal curing kiln at 50°C for st...
Embodiment 2
[0047] Example 2: Combining image 3 The mixture ratio is shown in Table 4.
[0048] Table 4, embodiment 2 mixture ratio
[0049]
[0050] Step 1: Add 25 kg of water, 8.7 kg of PVA solution, 15 kg of quartz sand powder, 5 kg of diatomaceous earth, 15 kg of lead-zinc tailings (1), 1.5 kg of gypsum and 7 kg of cement into the bucket in sequence and stir 5min;
[0051] Step 2: After adding 0.1 kg of water reducer, add 8 kg of lime and stir for 5 minutes;
[0052] Step 3: Add the mixed solution of 0.08 kg of aluminum powder and 0.025 kg of foam stabilizer to the slurry and stir for 3 minutes;
[0053] Step 4: Pour the slurry into the mold;
[0054] Step 5: Put the mold into the thermal curing kiln at 50°C for static maintenance;
[0055]Step 6: After 3-5 hours of static maintenance, demoulding and cutting of the aerated concrete body;
[0056] Step 7: After cutting, continue to put it into the thermal curing kiln at 50°C for static maintenance;
[0057] Step 8: Carry out...
Embodiment 3
[0058] Example 3: Binding image 3 The mixture ratio is shown in Table 5.
[0059] Table 5, embodiment 3 mixture ratio
[0060]
[0061] Step 1: Add 25 kg of water, 17.4 kg of PVA solution, 15 kg of quartz sand powder, 5 kg of diatomaceous earth, 15 kg of lead-zinc tailings, 1.5 kg of gypsum and 7 kg of cement into the bucket in order and stir for 5 minutes;
[0062] Step 2: After adding 0.1 kg of water reducer, add 8 kg of lime and stir for 5 minutes;
[0063] Step 3: Add the mixed solution of 0.08 kg of aluminum powder and 0.025 kg of foam stabilizer to the slurry and stir for 3 minutes;
[0064] Step 4: Pour the slurry into the mold;
[0065] Step 5: Put the mold into the thermal curing kiln at 50°C for static maintenance;
[0066] Step 6: After static maintenance for 3-5 hours, demoulding and cutting of aerated concrete body;
[0067] Step 7: After cutting, continue to put it into the thermal curing kiln at 50°C for static maintenance;
[0068] Step 8: Carry out a...
PUM
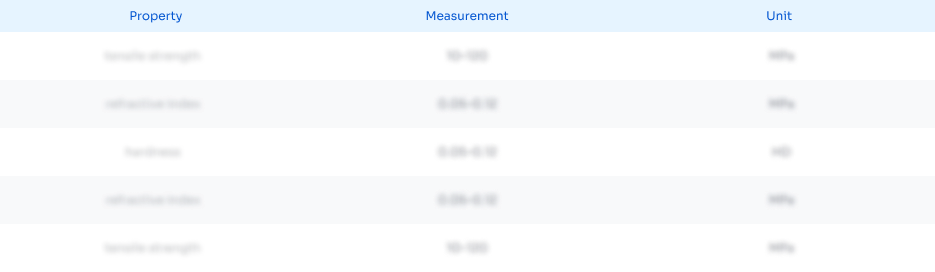
Abstract
Description
Claims
Application Information

- R&D
- Intellectual Property
- Life Sciences
- Materials
- Tech Scout
- Unparalleled Data Quality
- Higher Quality Content
- 60% Fewer Hallucinations
Browse by: Latest US Patents, China's latest patents, Technical Efficacy Thesaurus, Application Domain, Technology Topic, Popular Technical Reports.
© 2025 PatSnap. All rights reserved.Legal|Privacy policy|Modern Slavery Act Transparency Statement|Sitemap|About US| Contact US: help@patsnap.com