Method for preparing solid spherical rare earth oxide in one-step spraying thermal decomposition mode
A spray thermal decomposition, rare earth oxide technology, applied in rare earth metal compounds, chemical instruments and methods, inorganic chemistry, etc., can solve problems such as unbalanced decomposition, complex process control and equipment structure, and unavailability, and simplify the process. Parameter control and simplification of complex equipment structure, beneficial to industrial applications
- Summary
- Abstract
- Description
- Claims
- Application Information
AI Technical Summary
Problems solved by technology
Method used
Image
Examples
Embodiment 1
[0037] First, the temperature of the roasting furnace is controlled at 400°C, and then a solution containing 350 g / L cerium chloride and 10 g / L oxalic acid is mixed with carrier compressed air at a flow rate of 800 liters / hour and sprayed into the roasting furnace. Roasting for 20 seconds, the slag is naturally cooled to obtain a solid spherical powder product with a cerium oxide content greater than 90wt%, and its scanning electron microscope picture is as follows: figure 1 shown, from figure 1 It can be seen that the particle size of spherical cerium oxide is uniform, and the average particle size is nanometer; its XRD pattern is as follows figure 2 shown, from figure 2 It can be seen that there are no miscellaneous peaks of other elements in the spectrum, and the purity of the powder is high.
Embodiment 2
[0041] First, the temperature of the roaster is controlled at 600°C, and then the solution containing 280g / L lanthanum chloride and 0.1g / L citric acid is mixed with the carrier compressed oxygen at a flow rate of 80 liters / hour and sprayed into the roaster Within 60 seconds of roasting, the slag is naturally cooled to obtain a solid spherical powder product with a lanthanum oxide content greater than 90wt%, and its XRD pattern is as follows Figure 4 shown, from Figure 4 It can be seen that there are no miscellaneous peaks of other elements in the spectrum, and the powder has high purity. It is a spherical substance with uniform particle size detected by scanning electron microscope.
Embodiment 3
[0043] First, the temperature of the roasting furnace is controlled at 700°C, and then the solution containing praseodymium chloride with a concentration of 80g / L and ammonium carbonate with a concentration of 0.1g / L is mixed with carrier compressed air at a flow rate of 180 liters / hour and sprayed into the roaster Within 4 seconds of roasting, the slag is naturally cooled to obtain a solid spherical powder product with a praseodymium oxide content greater than 90wt%, and its XRD pattern is as follows Figure 5 shown, from Figure 5 It can be seen that there are no miscellaneous peaks of other elements in the spectrum, and the powder has high purity. It is a spherical substance with uniform particle size detected by scanning electron microscope.
PUM
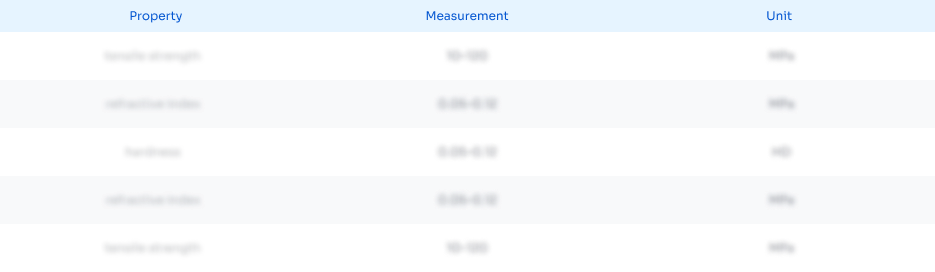
Abstract
Description
Claims
Application Information

- Generate Ideas
- Intellectual Property
- Life Sciences
- Materials
- Tech Scout
- Unparalleled Data Quality
- Higher Quality Content
- 60% Fewer Hallucinations
Browse by: Latest US Patents, China's latest patents, Technical Efficacy Thesaurus, Application Domain, Technology Topic, Popular Technical Reports.
© 2025 PatSnap. All rights reserved.Legal|Privacy policy|Modern Slavery Act Transparency Statement|Sitemap|About US| Contact US: help@patsnap.com