Supported catalyst for coal gasification and preparation method thereof
A supported catalyst and catalyst technology, applied in the direction of physical/chemical process catalysts, chemical instruments and methods, granular/powdered fuel gasification, etc., can solve the problems of catalyst activity reduction, alkali metal loss, deposition, adhesion, etc., to achieve Increase the chance of interaction, enhance catalytic activity, and enhance the effect of dispersion
- Summary
- Abstract
- Description
- Claims
- Application Information
AI Technical Summary
Problems solved by technology
Method used
Image
Examples
Embodiment 1
[0034] Preparation of embodiment 1 supported catalyst
[0035] 3.12g La(NO3 ) 3 , 1.48g Mn(NO 3 ) 2 , 0.35g Cu(NO 3 ) 2 Dissolve in 100ml of water respectively, and mix well after dissolving; then add citric acid with a ratio of 1:1 to the total number of metal ions in the solution, and continue to stir until fully dissolved; put the solution in a rotary evaporator at 45°C to evaporate and dehydrate until Form a gel-like substance; put the gel-like substance in a vacuum drying oven at 100°C and dry for 8 hours to form a porous solid; then bake and activate it in a muffle furnace at 750°C for 5 hours to obtain a composite oxide LaMn 0.8 Cu 0.2 o 3 ; Use the solution impregnation method to load the oxide on γ-Al 2 o 3 On the support, the oxide mass concentration is 20%, γ-Al 2 o 3 The mass concentration of the carrier is 75%, and it is dried and pretreated at 100°C, and roasted at 750°C; then, using the equal-volume impregnation method, K 2 CO 3 impregnated in γ-Al l...
Embodiment 2
[0036] Preparation of embodiment 2 supported catalyst
[0037] 3.12g La(NO 3 ) 3 , 0.93g Mn(NO 3 ) 2 , 0.87g Cu(NO 3 ) 2 Dissolve in 100ml of water respectively, and mix well after dissolving; then add citric acid with a ratio of 1:1 to the total number of metal ions in the solution, and continue to stir until fully dissolved; put the solution in a rotary evaporator at 45°C to evaporate and dehydrate until Form a gel-like substance; put the gel-like substance in a vacuum drying oven at 100°C and dry for 8 hours to form a porous solid; then bake and activate it in a muffle furnace at 700°C for 5 hours to obtain a composite oxide LaMn 0.6 Cu 0.4 o 3 ; Use the solution impregnation method to load the oxide on γ-Al 2 o 3 On the carrier, the oxide mass concentration is 30%, γ-Al 2 o 3 The mass concentration of the carrier is 60%, and it is dried and pretreated at 100°C, and roasted at 700°C; then, using the equal volume impregnation method, K 2 CO 3 impregnated in γ-Al...
Embodiment 3
[0038] Preparation of embodiment 3 supported catalyst
[0039] 3.12g La(NO 3 ) 3 , 1.85g Mn(NO 3 ) 2 Dissolve in 100ml of water respectively, and mix well after dissolving; then add citric acid with a total molar number of metal ions in the solution of 0.8:1, and continue to stir until fully dissolved; put the solution in a rotary evaporator to evaporate and dehydrate at 40°C until Form a gel-like substance; put the gel-like substance in a vacuum drying oven at 80°C and dry for 8 hours to form a porous solid; then bake and activate it in a muffle furnace at 500°C for 5 hours to obtain a composite oxide LaMnO 3 ; Use the solution impregnation method to load the oxide on γ-Al 2 o 3 On the carrier, the oxide mass concentration is 30%, γ-Al 2 o 3 The mass concentration of the carrier is 60%, and it is dried and pretreated at 80°C, and roasted at 500°C; then, using the equal-volume impregnation method, K 2 CO 3 impregnated in γ-Al loaded with composite oxide 2 o 3 and dr...
PUM
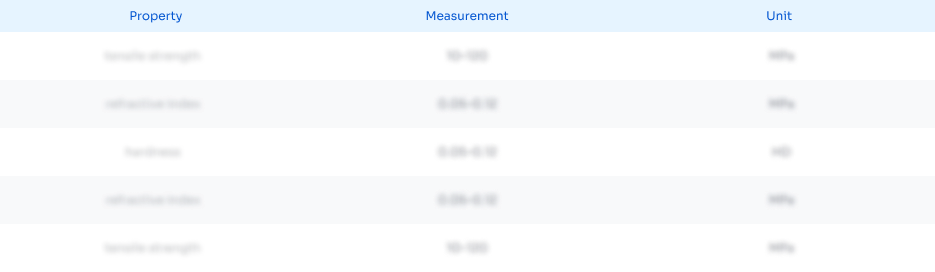
Abstract
Description
Claims
Application Information

- R&D
- Intellectual Property
- Life Sciences
- Materials
- Tech Scout
- Unparalleled Data Quality
- Higher Quality Content
- 60% Fewer Hallucinations
Browse by: Latest US Patents, China's latest patents, Technical Efficacy Thesaurus, Application Domain, Technology Topic, Popular Technical Reports.
© 2025 PatSnap. All rights reserved.Legal|Privacy policy|Modern Slavery Act Transparency Statement|Sitemap|About US| Contact US: help@patsnap.com