Sulfur-tolerant low-carbon alcohol catalyst and preparing method and application thereof
A technology for catalysts and low-carbon alcohols, applied in catalyst activation/preparation, chemical instruments and methods, preparation of hydroxyl compounds, etc., can solve the problems of low selectivity of higher alcohols, harsh reaction conditions, and high water content of products, and achieve high C2+ OH selectivity, easy industrial application, the effect of simplifying the preparation process
- Summary
- Abstract
- Description
- Claims
- Application Information
AI Technical Summary
Problems solved by technology
Method used
Image
Examples
Embodiment 1
[0039] At 60°C, with stirring, water and ethanol (H 2 O / C 2 h 5 OH=1:5) mixed solution is the citric acid solution of solvent preparation 0.4mol / L, adds concentrated hydrochloric acid and adjusts pH=3; Fe(NO 3 ) 3 9H 2 O and (NH 4 ) 6 Mo 7 o 24 4H 2 O is added respectively in the above-mentioned solution with Fe:Mo molar ratio 0.125:1, wherein citric acid: (M 1 +M 2 ) molar ratio is 1:1, and then the solution is heated in a water bath at 60°C; stirring is continued for 2 hours, and the obtained product is treated at 100°C for 12 hours to obtain a FeMo precursor, cooled to room temperature, and placed in a muffle Roast in the furnace at 500°C for 3h, cool to room temperature and take out. After the precursor was ground to 60-80 mesh, 1.0 g was taken and placed in a quartz tube reactor, and Ar was passed into the reactor at a flow rate of 100 ml / min. Using temperature programming control, the temperature rises from room temperature to 400°C at a rate of 5°C / min, and ...
Embodiment 2
[0041] At 60°C, with stirring, water and methanol (H 2 O / CH 3 OH=1:5) mixed solution is the citric acid solution of solvent preparation 0.4mol / L, adds concentrated hydrochloric acid and adjusts pH=3; Fe(NO 3 ) 3 9H 2 O and (NH 4 ) 6 Mo 7 o 24 4H 2 O is added in the above-mentioned solution respectively with Fe:Mo molar ratio 0.25:1, wherein citric acid: (M 1 +M 2 ) molar ratio is 1:1, and then the solution is heated in a water bath at 60°C; stirring is continued for 2 hours, and the obtained product is treated at 100°C for 12 hours to obtain a FeMo precursor, cooled to room temperature, and placed in a muffle Roast in the furnace at 600°C for 3h, cool to room temperature and take out. After the precursor was ground to 60-80 mesh, 1.0 g was taken and placed in a quartz tube reactor, and Ar was passed into the reactor at a flow rate of 100 ml / min. Using temperature programming control, the temperature rises from room temperature to 400°C at a rate of 5°C / min, and the ...
Embodiment 3
[0043] At 50°C, with stirring, water and ethanol (H 2 O / C 2 h 5 OH=1:5) mixed solution is the citric acid solution of solvent preparation 0.6mol / L, adds concentrated hydrochloric acid 1.5ml; Co(NO 3 ) 2 ·6H 2 O and (NH 4 ) 6 Mo 7 o 24 4H 2 O was added to the above solution with a Co:Mo molar ratio of 0.1:1, wherein citric acid: (M 1 +M 2 ) with a molar ratio of 1:6 and then place the solution in a 60°C water bath and heat it; continue to stir for 12 hours, and treat the resulting product at 100°C for 12 hours to obtain a CoMo precursor, cool it to room temperature, and then place it in a muffle furnace Calcined at 600°C for 3h, cooled to room temperature and taken out. After the precursor was ground to 60-80 mesh, 1.0 g was taken and placed in a quartz tube reactor, and Ar was passed into the reactor at a flow rate of 100 ml / min. Using temperature programming control, the temperature rises from room temperature to 400°C at a rate of 5°C / min, and the temperature ris...
PUM
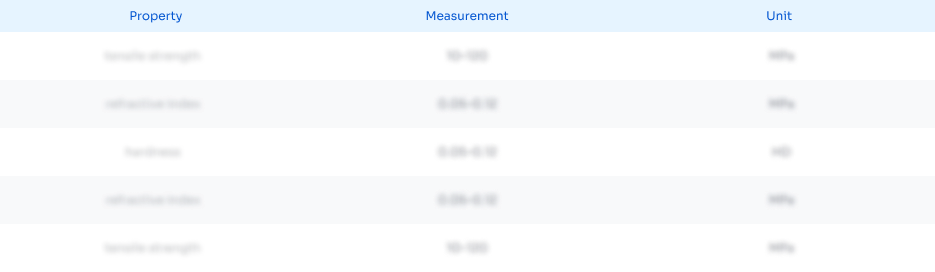
Abstract
Description
Claims
Application Information

- R&D
- Intellectual Property
- Life Sciences
- Materials
- Tech Scout
- Unparalleled Data Quality
- Higher Quality Content
- 60% Fewer Hallucinations
Browse by: Latest US Patents, China's latest patents, Technical Efficacy Thesaurus, Application Domain, Technology Topic, Popular Technical Reports.
© 2025 PatSnap. All rights reserved.Legal|Privacy policy|Modern Slavery Act Transparency Statement|Sitemap|About US| Contact US: help@patsnap.com