Quench cooling process for H13 steel
A cooling process and workpiece technology, applied in the direction of quenching agent, manufacturing tools, heat treatment equipment, etc., can solve problems such as cracking and deformation, and achieve the effect of slowing down cooling speed, reducing tissue stress, and not deep cracking
- Summary
- Abstract
- Description
- Claims
- Application Information
AI Technical Summary
Problems solved by technology
Method used
Image
Examples
Embodiment 1
[0028] The gas quenching furnace adopts a vacuum pressure gas quenching furnace, which is evacuated to a pressure of 0.08Pa in the furnace, and then filled with N with a pressure of 100Pa. 2 Carry out protection; heat up at a heating rate of 15°C / min, and keep warm for 200 minutes when the furnace temperature reaches 650°C; then continue heating at a heating rate of 13°C / min, and keep warm for 140 minutes when it reaches 850°C; Heating at a heating rate of 13°C / min, keeping warm at 1050°C for 135min; filling the vacuum high-pressure gas quenching furnace with N 2 , the workpiece is cooled to a surface temperature of 680 °C; the workpiece is taken out and quenched into a 50% sodium hydroxide aqueous solution and cooled to a surface temperature of 370 °C; the workpiece is taken out of the aqueous solution and isothermal until the difference between the core temperature and the surface temperature of the workpiece The temperature is less than 90°C, and then the workpiece is air-c...
Embodiment 2
[0030] The gas quenching furnace adopts a vacuum pressure gas quenching furnace, which is evacuated to a pressure of 0.08Pa in the furnace, and then filled with N with a pressure of 100Pa. 2 Carry out protection; heat up at a heating rate of 15°C / min, and keep warm for 200 minutes when the furnace temperature reaches 650°C; then continue heating at a heating rate of 13°C / min, and keep warm for 140 minutes when it reaches 850°C; Heating at a heating rate of 13°C / min, keeping warm at 1050°C for 135min; filling the vacuum high-pressure gas quenching furnace with N 2 , the workpiece is cooled to a surface temperature of 720°C; the workpiece is taken out and quenched into a 50% sodium hydroxide aqueous solution and cooled to a surface temperature of 410°C; the workpiece is taken out of the aqueous solution and isothermal until the difference between the core temperature and the surface temperature of the workpiece The temperature is less than 90°C, and then the workpiece is air-coo...
Embodiment 3
[0032] The gas quenching furnace adopts a vacuum pressure gas quenching furnace, which is evacuated to a pressure of 0.08Pa in the furnace, and then filled with N with a pressure of 100Pa. 2 Carry out protection; heat up at a heating rate of 15°C / min, and keep warm when the furnace temperature reaches 650°C for 200 minutes; then continue heating at a heating rate of 13°C / min, and keep warm when it reaches 850°C for 140 minutes; Heating at a heating rate of 13°C / min, keeping warm at 1050°C for 135min; filling the vacuum high-pressure gas quenching furnace with N 2 , the workpiece is cooled to a surface temperature of 700°C; the workpiece is taken out and quenched into a 50% sodium hydroxide aqueous solution and cooled to a surface temperature of 390°C; the workpiece is taken out of the aqueous solution and isothermal until the difference between the core temperature and the surface temperature of the workpiece The temperature is less than 90°C, and then the workpiece is air-coo...
PUM
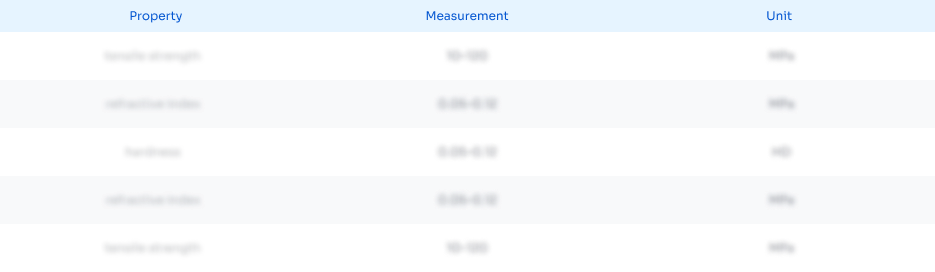
Abstract
Description
Claims
Application Information

- R&D
- Intellectual Property
- Life Sciences
- Materials
- Tech Scout
- Unparalleled Data Quality
- Higher Quality Content
- 60% Fewer Hallucinations
Browse by: Latest US Patents, China's latest patents, Technical Efficacy Thesaurus, Application Domain, Technology Topic, Popular Technical Reports.
© 2025 PatSnap. All rights reserved.Legal|Privacy policy|Modern Slavery Act Transparency Statement|Sitemap|About US| Contact US: help@patsnap.com