Bio-enzyme pretreatment method of pure cotton fabric
A pure cotton fabric and biological enzyme technology, applied in the field of pure cotton fabric biological enzyme pretreatment, can solve the problems of strong metal corrosion, limited use, high energy consumption, etc., and achieve short process flow, small fabric damage and mild treatment conditions Effect
- Summary
- Abstract
- Description
- Claims
- Application Information
AI Technical Summary
Problems solved by technology
Method used
Examples
Embodiment 1
[0033] (1) Preparation of compound biological enzyme
[0034] Weigh 15 parts by weight of cutinase, 40 parts by weight of alkaline pectinase, 15 parts by weight of 1,4-B-D-glucose-4-glucoside hydrolase and 30 parts by weight of laccase, stir and mix evenly to obtain The compound biological enzyme.
[0035] (2) Preparation of scouring bleaching solution
[0036] At room temperature, add compound biological enzyme, hydrogen peroxide, tetraacetylethylenediamine, babassu oleamide propylamine oxide and sodium chloride into water, stir and mix evenly to obtain a scouring bleaching solution, the scouring bleaching Liquid, composed of the following components by weight percentage: 3% of the compound biological enzyme, 7.5% hydrogen peroxide, 1.5% tetraacetylethylenediamine, 0.2% babassu oleamide propylamine oxide, 0.2% sodium chloride %, the balance is water.
[0037] (3) Scouring and bleaching in the same bath
[0038] The pure cotton fabric is added into the scouring and bleachi...
PUM
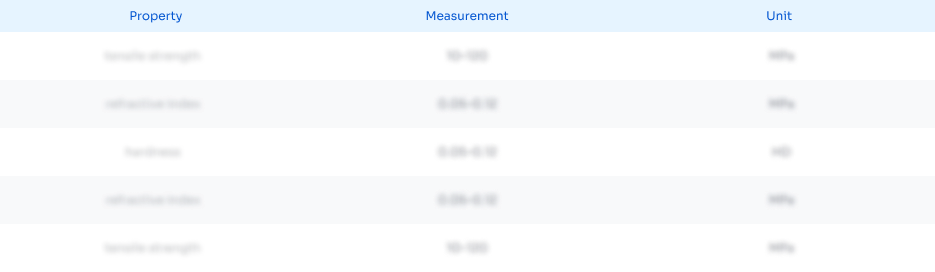
Abstract
Description
Claims
Application Information

- R&D
- Intellectual Property
- Life Sciences
- Materials
- Tech Scout
- Unparalleled Data Quality
- Higher Quality Content
- 60% Fewer Hallucinations
Browse by: Latest US Patents, China's latest patents, Technical Efficacy Thesaurus, Application Domain, Technology Topic, Popular Technical Reports.
© 2025 PatSnap. All rights reserved.Legal|Privacy policy|Modern Slavery Act Transparency Statement|Sitemap|About US| Contact US: help@patsnap.com