Formula and preparation process of a machine tool working fluid
A machine tool working fluid and process technology, applied in the petroleum industry, lubricating composition, etc., can solve the problems of quality decline, efficiency decline, affecting the subsequent processing of parts, etc., and achieve the effect of long effective time, easy cleaning and strong versatility
- Summary
- Abstract
- Description
- Claims
- Application Information
AI Technical Summary
Problems solved by technology
Method used
Examples
Embodiment 1
[0050] A formula for machine tool working fluid; this formula contains the following substances:
[0051] 10 parts of dodecenyl succinic acid; 5 parts of sodium petroleum sulfonate; 5 parts of alkylphenol polyoxyethylene ether; 2 parts of edible sodium benzoate; 5 parts of polyethylene glycol; 2 parts of sodium phosphate; 5 parts of barium petroleum sulfonate 5 parts of triethanolammonium; 5 parts of sodium lauryl sulfate; 2 parts of ethylenediaminetetraacetic acid; 1 part of rosin; 1 part of defoamer; 52 parts of deionized water.
[0052] A preparation process of machine tool working fluid, comprising the following steps:
[0053] Step 1: Mix and stir 5 parts of triethanolammonium, 5 parts of barium petroleum sulfonate, 10 parts of dodecenyl succinic acid, and 5 parts of sodium petroleum sulfonate, stir and heat to 80°C, keep warm for 1 hour, and the temperature drops to 30°C ;
[0054] Step 2: Add 5 parts of polyethylene glycol, 2 parts of sodium phosphate, 2 parts of edib...
Embodiment 2
[0058] A formula for machine tool working fluid; this formula contains the following substances:
[0059] 20 parts of dodecenyl succinic acid; 10 parts of sodium petroleum sulfonate; 7 parts of alkylphenol polyoxyethylene ether; 6 parts of edible sodium benzoate; 7 parts of polyethylene glycol; 7 parts of sodium phosphate; 10 parts of barium petroleum sulfonate 8 parts of triethanolammonium; 8 parts of sodium lauryl sulfate; 4 parts of ethylenediaminetetraacetic acid; 3 parts of rosin; 2 parts of defoamer; 8 parts of deionized water.
[0060] A preparation process of machine tool working fluid, comprising the following steps:
[0061] Step 1: Mix and stir 8 parts of triethanolammonium, 10 parts of barium petroleum sulfonate, 20 parts of dodecenyl succinic acid, and 10 parts of sodium petroleum sulfonate, stir and heat to 100°C, keep warm for 3 hours, and the temperature drops to 50°C ;
[0062] Step 2: Add 7 parts of polyethylene glycol, 7 parts of sodium phosphate, 6 parts ...
Embodiment 3
[0066] A formula for machine tool working fluid; this formula contains the following substances:
[0067] 10 parts of dodecenyl succinic acid; 10 parts of sodium petroleum sulfonate; 5 parts of alkylphenol polyoxyethylene ether; 6 parts of edible sodium benzoate; 5 parts of polyethylene glycol; 7 parts of sodium phosphate; 10 parts of barium petroleum sulfonate 5 parts of triethanolammonium; 8 parts of sodium lauryl sulfate; 4 parts of ethylenediaminetetraacetic acid; 1 part of rosin; 1 part of defoamer; 28 parts of deionized water.
[0068] A preparation process of machine tool working fluid, which comprises the following steps:
[0069] Step 1: Mix and stir 5 parts of triethanolammonium, 10 parts of barium petroleum sulfonate, 10 parts of dodecenyl succinic acid, and 10 parts of sodium petroleum sulfonate, stir and heat to 80°C, keep warm for 3 hours, and the temperature drops to 50°C ;
[0070] Step 2: Add 5 parts of polyethylene glycol, 7 parts of sodium phosphate, 6 par...
PUM
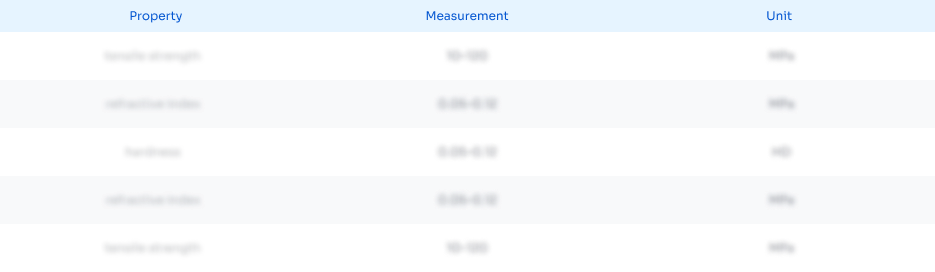
Abstract
Description
Claims
Application Information

- Generate Ideas
- Intellectual Property
- Life Sciences
- Materials
- Tech Scout
- Unparalleled Data Quality
- Higher Quality Content
- 60% Fewer Hallucinations
Browse by: Latest US Patents, China's latest patents, Technical Efficacy Thesaurus, Application Domain, Technology Topic, Popular Technical Reports.
© 2025 PatSnap. All rights reserved.Legal|Privacy policy|Modern Slavery Act Transparency Statement|Sitemap|About US| Contact US: help@patsnap.com