Preparation method of iron oxide cathode material for lithium ion battery
A technology for lithium ion batteries and negative electrode materials, which is applied in the directions of iron oxide, battery electrodes, iron oxide/iron hydroxide, etc., to achieve the effects of simple preparation process, convenient large-scale production, and improved cycle stability
- Summary
- Abstract
- Description
- Claims
- Application Information
AI Technical Summary
Problems solved by technology
Method used
Image
Examples
Embodiment 1
[0027] Weigh 4.8663 g of inorganic iron salt, dissolve it in 100 ml of absolute ethanol, add 5.4 ml of deionized water, and stir evenly to form an orange-yellow solution; under stirring conditions, add 20.97 ml of propylene oxide dropwise to the solution, and stir evenly After a certain period of time, a gel was formed after standing; add absolute ethanol to the gel for aging, replace the absolute ethanol every 24 h, repeat 3 times; dry the gel at room temperature for 2 days, and then put it in 80 o C oven dried for 2 days to obtain the precursor product. Under the air atmosphere, the temperature of the precursor product was raised to 600 oC for 3 h, and cooled to room temperature with the furnace to prepare nano-iron oxide negative electrode material powder. The prepared 70 wt.% iron oxide material, 15 wt.% acetylene black and 15 wt.% PVdF were mixed evenly to make a slurry, which was uniformly coated on the copper foil, and punched into a circle after vacuum drying. Shaped...
Embodiment 2
[0030] Weigh 4.8663 g of inorganic iron salt, dissolve it in 60 ml of absolute ethanol, add 8.1 ml of deionized water, and stir evenly to form an orange-yellow solution; under stirring conditions, add 16.25 ml of propylene oxide dropwise to the solution, and stir evenly After a certain period of time, a gel was formed after standing; add absolute ethanol to the gel for aging, replace the absolute ethanol every 24 h, repeat 3 times; dry the gel at room temperature for 2 days, and then put it in 100 o C oven dried for 2 days to obtain the precursor product. Under the air atmosphere, the temperature of the precursor product was raised to 600 o C for 3 h, and cooled to room temperature with the furnace to prepare nano-iron oxide negative electrode material powder. The prepared 70 wt.% iron oxide material, 15 wt.% acetylene black and 15 wt.% PVdF were mixed evenly to make a slurry, which was uniformly coated on the copper foil, and punched into a circle after vacuum drying. Shape...
Embodiment 3
[0033] Weigh 4.8663 g of inorganic iron salt, dissolve it in 100 ml of absolute ethanol, add 5.4 ml of deionized water, and stir evenly to form an orange-yellow solution; under stirring conditions, add 24.12 ml of propylene oxide dropwise to the solution, and stir evenly After a certain period of time, a gel was formed after standing; add absolute ethanol to the gel for aging, replace the absolute ethanol every 24 h, repeat 3 times; dry the gel at room temperature for 2 days, and then put it in 80 o C oven dried for 2 days to obtain the precursor product. Under the air atmosphere, the temperature of the precursor product was raised to 800 o C for 3 h, and cooled to room temperature with the furnace to prepare nano-iron oxide negative electrode material powder. The prepared 70 wt.% iron oxide material, 15 wt.% acetylene black and 15 wt.% PVdF were mixed evenly to make a slurry, which was uniformly coated on the copper foil, and punched into a circle after vacuum drying. Shape...
PUM
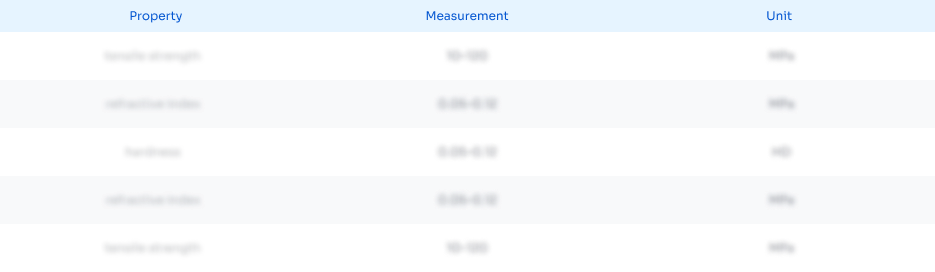
Abstract
Description
Claims
Application Information

- R&D Engineer
- R&D Manager
- IP Professional
- Industry Leading Data Capabilities
- Powerful AI technology
- Patent DNA Extraction
Browse by: Latest US Patents, China's latest patents, Technical Efficacy Thesaurus, Application Domain, Technology Topic, Popular Technical Reports.
© 2024 PatSnap. All rights reserved.Legal|Privacy policy|Modern Slavery Act Transparency Statement|Sitemap|About US| Contact US: help@patsnap.com