Method and device for continuous preparation of carbamyl chloride
A carbamoyl chloride and reaction device technology, which is applied in the preparation of carbamic acid derivatives, chemical methods for reacting gas medium with gas medium, chemical instruments and methods, etc., can solve the problem of high product yield, equipment utilization, and continuous industrialization Production and low utilization of equipment, etc., to achieve good mixing effect, easy to enlarge production capacity, and high utilization of equipment
- Summary
- Abstract
- Description
- Claims
- Application Information
AI Technical Summary
Problems solved by technology
Method used
Image
Examples
Embodiment 1
[0025] The mixture of phosgene and nitrogen is preheated to 210°C by the preheater 1, and enters the tubular reactor from the tangential direction through the phosgene inlet 4. The mixture of monomethylamine and nitrogen is preheated to 190°C by the preheater 2, enters the three membrane tube channels 6 of the ceramic membrane microporous gas distributor through the amino compound inlet 3, and then enters the tubular reactor to mix with the amino compound. The ratio of phosgene to monomethylamine is 1.3:1. Control the temperature of the tubular reactor at 200-400°C for reaction. The residence time is 3s, and the reaction product flows out through the reaction product discharge pipe 7 of the tubular reactor. The prepared intermediate is converted into methyl isocyanate by existing industrial methods, and the yield of methyl isocyanate is 98.1%.
Embodiment 2
[0027] The mixture of phosgene and nitrogen is preheated to 190°C by the preheater 1, and enters the tubular reactor from the tangential direction through the phosgene inlet 4. The mixture of monomethylamine and nitrogen is preheated to 210°C by the preheater 2, enters the five membrane tube channels 6 of the ceramic membrane microporous gas distributor through the amino compound inlet 3, and then enters the tubular reactor to mix with the amino compound. The ratio of phosgene to monomethylamine is 1.15:1. Control the temperature of the tubular reactor at 200-400°C for reaction. The residence time is 8 s, and the reaction product flows out through the reaction product discharge pipe 7 of the tubular reactor. The prepared intermediate is converted into methyl isocyanate by existing industrial methods, and the yield of methyl isocyanate is 97.5%.
Embodiment 3
[0029] The mixture of phosgene and nitrogen is preheated to 190°C by the preheater 1, and enters the tubular reactor from the tangential direction through the phosgene inlet 4. The mixture of monomethylamine and nitrogen is preheated to 210°C by the preheater 2, enters the five membrane tube channels 6 of the ceramic membrane microporous gas distributor through the amino compound inlet 3, and then enters the tubular reactor to mix with the amino compound. The ratio of phosgene to monomethylamine is 1.2:1. Control the temperature of the tubular reactor at 200-350°C for reaction. The residence time is 2.6 s, and the reaction product flows out through the reaction product discharge pipe 7 of the tubular reactor. The prepared intermediate is converted into methyl isocyanate by existing industrial methods, and the yield of methyl isocyanate is 99.1%.
PUM
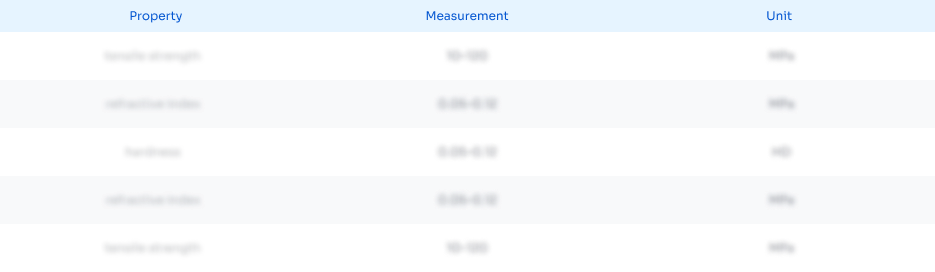
Abstract
Description
Claims
Application Information

- Generate Ideas
- Intellectual Property
- Life Sciences
- Materials
- Tech Scout
- Unparalleled Data Quality
- Higher Quality Content
- 60% Fewer Hallucinations
Browse by: Latest US Patents, China's latest patents, Technical Efficacy Thesaurus, Application Domain, Technology Topic, Popular Technical Reports.
© 2025 PatSnap. All rights reserved.Legal|Privacy policy|Modern Slavery Act Transparency Statement|Sitemap|About US| Contact US: help@patsnap.com