Recovering process of solvent tertiary butanol in production process of ammoximation
A production process and technology of tert-butanol, applied in the preparation/separation of ammonia, preparation of organic compounds, organic chemistry, etc., can solve the problems of increasing the cost of vacuum compression, adverse effects on product performance at the bottom of the column, and low temperature of the gas at the top of the column.
- Summary
- Abstract
- Description
- Claims
- Application Information
AI Technical Summary
Problems solved by technology
Method used
Image
Examples
Embodiment 1
[0028] Two-effect parallel rectification process of tert-butanol rectification tower, such as figure 1 As shown, the reaction liquid from the reactor enters the flash tank 1 for adiabatic flash evaporation. The operating pressure of the flash tank is normal pressure. Material preheater 3, the temperature of the material after preheating is 84 ℃, under the control of the flow rate, it is respectively sent to the middle part of the first-effect rectification tower 4 and the middle part of the second-effect rectification tower 6, and the first-effect rectification tower 4 The operating pressure is 0.3MPa (absolute pressure), the temperature at the top of the tower is 107°C, and the temperature at the bottom of the tower is 137°C. The reboiler 5 of the tower is heated by low-pressure steam, and part of the reaction liquid is vaporized in the reboiler. Separation occurs, and the materials in the tower kettle that meet the separation requirements are sent to the feed preheater 3 to ...
Embodiment 2
[0033] Two-effect countercurrent series rectification process of tert-butanol rectification tower, such as figure 2 As shown, the reaction liquid from the reactor enters the flash tank 1 for adiabatic flash evaporation. The operating pressure of the flash tank is normal pressure. Material preheater 3, the temperature of the material after preheating is 82°C, and enters the middle part of the second-effect rectification tower 6, the operating pressure in the tower is 0.045MPa (absolute pressure), the temperature at the top of the tower is 57°C, and the temperature at the bottom of the tower is 67 ℃, the reboiler 7 of the tower kettle is heated by first-effect steam, the reaction liquid is vaporized in the reboiler, rectified and separated in the tower, and after preliminary separation, the gas enters the cooling system from the top of the tower, and the reaction liquid after preliminary separation is Under the control of the flow rate, the discharge pump 9 of the second-effect...
Embodiment 3
[0038] Two-effect co-current series rectification process of tert-butanol rectification tower, such as image 3 As shown, the reaction liquid from the reactor enters the flash tank 1 for adiabatic flash evaporation, the operating pressure of the flash tank is normal pressure, the gas phase after flash evaporation enters the cooling system, and the liquid phase enters a In the middle part of the efficient rectification tower 4, the operating pressure in the tower is 0.25MPa (absolute pressure), the temperature at the top of the tower is 85°C, and the temperature at the bottom of the tower is 110°C. Internal gasification, rectification and separation in the tower, the gas phase at the top of the first-effect rectification tower 4 is discharged to the condensation side of the reboiler 7 of the second-effect rectification tower 6, and most of the gas phase is on the condensation side of the reboiler 7 Condensation, the liquid phase enters the reflux system, and the gas phase enter...
PUM
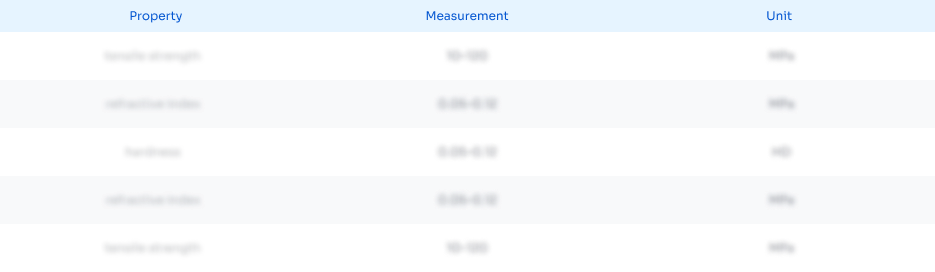
Abstract
Description
Claims
Application Information

- R&D Engineer
- R&D Manager
- IP Professional
- Industry Leading Data Capabilities
- Powerful AI technology
- Patent DNA Extraction
Browse by: Latest US Patents, China's latest patents, Technical Efficacy Thesaurus, Application Domain, Technology Topic, Popular Technical Reports.
© 2024 PatSnap. All rights reserved.Legal|Privacy policy|Modern Slavery Act Transparency Statement|Sitemap|About US| Contact US: help@patsnap.com