Duplex stainless steel with excellent thermoplasticity and corrosion resistance and manufacturing method thereof
A technology of duplex stainless steel and a manufacturing method, applied in the field of duplex stainless steel, can solve the problem of difficult to avoid edge cracking during hot rolling, and achieve the effects of reducing adverse effects, improving thermoplasticity, good thermoplasticity and cold workability
- Summary
- Abstract
- Description
- Claims
- Application Information
AI Technical Summary
Problems solved by technology
Method used
Image
Examples
Embodiment 1
[0056] Take the production process of vacuum smelting - die casting - forging - hot rolling - annealing and pickling as an example: the raw materials are added to the vacuum smelting furnace for smelting, and the purity of the raw materials is strictly controlled to obtain the design components (as shown in Table 1); Pour it into a casting mold to obtain a 50Kg steel ingot, and the casting superheat degree is 20-50°C. The ingot is forged, the forging heating temperature is 1100-1250°C, and the thickness after forging is 40 mm. The forging billet was rolled on a reversing hot rolling mill with a heating temperature of 1100-1200° C., rolled to 4 mm, and the edge crack after hot rolling was measured. The hot-rolled sheet is annealed, the annealing temperature is controlled at 1020-1100°C, and the proportion of austenite in the structure after annealing is 40-60%, to obtain the duplex stainless steel with excellent thermoplasticity and corrosion resistance in this example.
[005...
Embodiment 2~8
[0062] The duplex stainless steels of Examples 2 to 8 were produced according to the production method of Example 1.
[0063] The alloy chemical composition of the duplex stainless steel in each example is shown in Table 1.
[0064] The duplex stainless steel material of each embodiment was tested for corrosion resistance, and its corrosion resistance was characterized by CPT (critical pitting temperature), and the measurement standard was ASTM G48-99.
[0065]Detect the duplex stainless steel of each embodiment to obtain the metallographic structure of the alloy of each embodiment: after the sample is ground and polished, electrolytic corrosion is carried out, and the corrosive agent is 40g KOH+100ml H 2 O, corrosion current 0.3~0.8A / cm 2 Finally, the proportion of austenite is analyzed by quantitative metallographic method under the metallographic microscope; the black structure is ferrite, the white structure is austenite, and the austenite phase accounts for 40-60%.
[0...
PUM
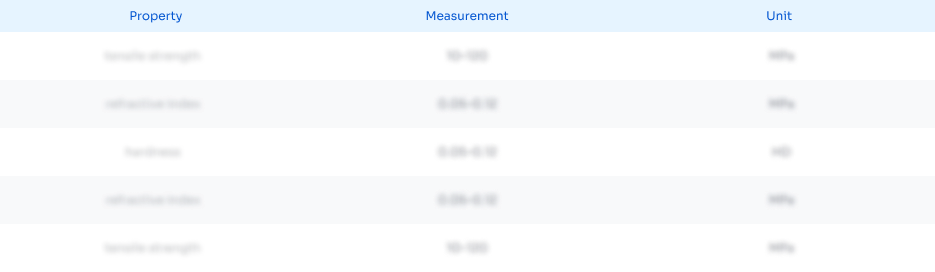
Abstract
Description
Claims
Application Information

- Generate Ideas
- Intellectual Property
- Life Sciences
- Materials
- Tech Scout
- Unparalleled Data Quality
- Higher Quality Content
- 60% Fewer Hallucinations
Browse by: Latest US Patents, China's latest patents, Technical Efficacy Thesaurus, Application Domain, Technology Topic, Popular Technical Reports.
© 2025 PatSnap. All rights reserved.Legal|Privacy policy|Modern Slavery Act Transparency Statement|Sitemap|About US| Contact US: help@patsnap.com