Polymer bonded explosive for missile of common jet hole
A technology for bonding explosives and perforating charges, which is applied to explosives, non-explosive/non-thermal components, nitrated acyclic/alicyclic/heterocyclic amine explosive compositions, etc., can solve the problem of low energy and strength, safety High energy, simple process and low mechanical sensitivity
- Summary
- Abstract
- Description
- Claims
- Application Information
AI Technical Summary
Problems solved by technology
Method used
Image
Examples
Embodiment 1
[0017] (1) Take materials according to the following components by weight percentage: 98% of RDX, 1.7% of ethylene-vinyl acetate copolymer, and 0.3% of colloidal graphite.
[0018] (2) Preparation
[0019] Add 1960g of Hexogen and 3000ml of water, then add 34g of ethylene-vinyl acetate copolymer emulsion, stir for 10min, heat up to about 60-65℃, add 40g of anhydrous sodium sulfate, stir for 5min, the sodium sulfate dissolves and destroys the emulsion, Precipitate ethylene-vinyl acetate copolymer, add about 300ml of toluene, heat up to 65°C, stir for about 5-10min to form particles. Toluene was distilled off under reduced pressure. Cool to below 40°C and discharge, after filtration, washing, drying and screening, white granules are obtained. In a mixer, mix the white particles with 6g of colloidal graphite evenly to obtain gray-black modeling powder.
[0020] (3) Performance test
[0021] The performance test data is shown in Table 1 below:
[0022] Table 1 performance tes...
Embodiment 2
[0027] The implementation is carried out with reference to the following mass percentage composition: 96.5% of RDX, 3% of ethylene-vinyl acetate copolymer, and 0.5% of graphite.
[0028] The preparation process of this embodiment refers to Example 1, and the performance test results are basically the same, but the detonation velocity is slightly reduced, and the detonation velocity is 8437m / s (1.726g / cm 3 )
Embodiment 3
[0030] The implementation is carried out with reference to the following mass percentage composition: 95% of RDX, 4% of ethylene-vinyl acetate copolymer, and 1% of graphite.
[0031] The preparation process of this embodiment refers to Example 1, and the performance test results are basically the same, but the detonation velocity is slightly reduced, and the detonation velocity is 8353m / s (1.710g / cm 3 )
PUM
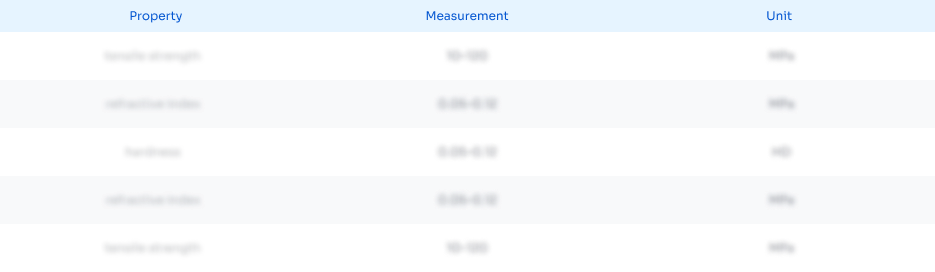
Abstract
Description
Claims
Application Information

- R&D Engineer
- R&D Manager
- IP Professional
- Industry Leading Data Capabilities
- Powerful AI technology
- Patent DNA Extraction
Browse by: Latest US Patents, China's latest patents, Technical Efficacy Thesaurus, Application Domain, Technology Topic, Popular Technical Reports.
© 2024 PatSnap. All rights reserved.Legal|Privacy policy|Modern Slavery Act Transparency Statement|Sitemap|About US| Contact US: help@patsnap.com