Preparation method of zirconium silicate wrapped ceramic pigment
A ceramic coloring material and wrapping technology, which is applied in the field of ceramic coloring materials, can solve the problems of reducing the protective effect of the coating layer on the color material particles, the loose structure of the coating layer, and the destruction of the structure of the coating layer, so as to improve the color rendering effect and stability , Improve the color rendering effect and avoid the effect of damage
- Summary
- Abstract
- Description
- Claims
- Application Information
AI Technical Summary
Problems solved by technology
Method used
Image
Examples
Embodiment 1
[0028] In this embodiment, a method for preparing a zirconium silicate-wrapped ceramic pigment is used to prepare a wrapped carbon black material. The steps are as follows:
[0029] (1) Preparation of raw material solution
[0030] SiO 2 -ZrO 2 Mixed gel: 21 mL of ZrO with a concentration of 0.917 mol / L was mixed under vigorous stirring 2 The sol was dripped into 20mL of SiO with a concentration of 1.3mol / L 2 sol, mixed uniformly to obtain SiO 2 -ZrO 2 Mixed glue;
[0031] Suspension A: use 6ml carbon ink as suspension A;
[0032] Aluminum nitrate solution: take 2ml of concentrated nitric acid, stir and add 3.5g of aluminum nitrate, then add 3ml of distilled water to obtain an aluminum nitrate solution;
[0033] (2) Add the above suspension A to the above SiO 2 -ZrO 2 Mix evenly in the mixed sol to obtain precursor suspension B;
[0034] (3) adding the above-mentioned aluminum nitrate solution to the precursor suspension B to form the precursor suspension C;
[0035...
Embodiment 2
[0039] The preparation method of a zirconium silicate-wrapped ceramic colorant in this example differs from Example 1 in that: step (4) the precursor suspension C is dried in a spray drying tower, and the drying temperature is 200 ° C; the step ( In 5), the powdery precursor D was placed in a tube furnace protected by an Ar atmosphere, and calcined at a temperature of 1100°C for 2 hours to obtain a zirconium silicate-coated carbon black material, and the L* value of the color material was 13.2.
[0040]Remove the unwrapped carbon black, and the L* value of the wrapped carbon black material is 28. After it is mixed with the transparent glaze according to the mass ratio color material: transparent glaze = 1:5, it is calcined at 800 ° C for 20 minutes, and the obtained The L* value of the glaze is 37.5.
Embodiment 3
[0042] In this embodiment, a method for preparing a zirconium silicate-wrapped ceramic pigment is used to prepare a wrapped cadmium-selenium red material, and the steps are as follows:
[0043] (1) Preparation of raw material solution
[0044] SiO 2 -ZrO 2 Mixed gel: 21 mL of ZrO with a concentration of 0.917 mol / L was stirred 2 The sol was dripped into 21 mL of SiO with a concentration of 1.04 mol / L 2 Mixed homogeneously in the sol to obtain SiO 2 -ZrO 2 Mixed glue;
[0045] Suspension A: Add 5g of commercially available cadmium-selenium red material to 45mL of absolute ethanol, ultrasonically disperse for 2 minutes, take another 45mL of absolute ethanol, add 5mL of PEG (molecular weight 600), and mix well; the ethanol suspension of cadmium-selenium red Add to the PEG-ethanol mixed solution, mix ultrasonically for 2 minutes, and ball mill for 1 hour to obtain a stable suspension A;
[0046] Aluminum nitrate solution: take 2ml of concentrated nitric acid, stir and add 1...
PUM
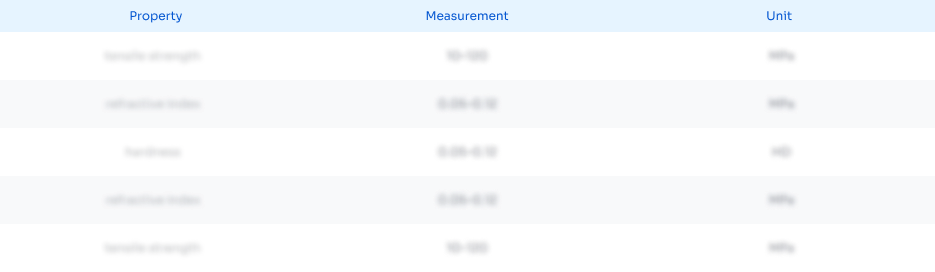
Abstract
Description
Claims
Application Information

- Generate Ideas
- Intellectual Property
- Life Sciences
- Materials
- Tech Scout
- Unparalleled Data Quality
- Higher Quality Content
- 60% Fewer Hallucinations
Browse by: Latest US Patents, China's latest patents, Technical Efficacy Thesaurus, Application Domain, Technology Topic, Popular Technical Reports.
© 2025 PatSnap. All rights reserved.Legal|Privacy policy|Modern Slavery Act Transparency Statement|Sitemap|About US| Contact US: help@patsnap.com