Preparation technology of copper-clad laminate based on halogen-free flame-retardant resin compositions
A technology of copper-clad laminates and flame-retardant resins, applied in lamination, lamination devices, layered products, etc., can solve the problem of affecting the service life of plates and finished products, failing to meet the requirements of lead-free soldering, and reducing flame retardancy Solve the problems such as the moisture absorption performance of the agent, and achieve the effect of high CTI performance, high reliability and excellent processability
- Summary
- Abstract
- Description
- Claims
- Application Information
AI Technical Summary
Problems solved by technology
Method used
Image
Examples
Embodiment 1
[0027] A preparation process of a copper-clad laminate based on a halogen-free flame-retardant resin composition, comprising the following steps:
[0028] 1) Production of fabric glue: 70 parts of bisphenol A epoxy resin, 30 parts of o-cresol novolac epoxy resin, 2.8 parts of dicyandiamide, 30 parts of phenolic tripolyphosphazene, 35 parts of boehmite, 2 - 0.2 parts of ethyl-4 methylimidazole and 95 parts of DMF, prepared into a glue;
[0029] 2) Preparation of glue A: 20 parts of water-soluble phenolic resin, 80 parts of phenoxytripolyphosphazene, 750 parts of acetone and 80 parts of water, prepared into glue;
[0030] 3) Preparation of glue B: 30 parts of bisphenol A epoxy resin, 20 parts of o-cresol novolac epoxy resin, 50 parts of phosphorus-containing epoxy resin, 25 parts of bisphenol F benzoxazine resin, cardanol modified 10 parts of phenolic resin, 5 parts of phenoxytripolyphosphazene, 100 parts of aluminum hydroxide, 0.2 parts of 2-ethyl-4 methylimidazole and 105 par...
Embodiment 2
[0034] 1) Production of fabric glue: 70 parts of bisphenol A epoxy resin, 30 parts of o-cresol novolac epoxy resin, 2.8 parts of dicyandiamide, 30 parts of phenolic tripolyphosphazene, 30 parts of boehmite, 2 - 0.1 part of ethyl-4 methylimidazole and 90 parts of DMF, prepared into a glue;
[0035] 2) Preparation of glue A: 20 parts of water-soluble phenolic resin, 80 parts of phenoxytripolyphosphazene, 750 parts of acetone and 80 parts of water, prepared into glue;
[0036] 3) Production of glue B: 70 parts of bisphenol A epoxy resin, 30 parts of o-cresol novolak epoxy resin, 25 parts of bisphenol F benzoxazine resin, 10 parts of cardanol modified phenolic resin, phenoxy 35 parts of tripolyphosphazene, 70 parts of aluminum hydroxide, 0.2 part of 2-ethyl-4 methylimidazole and 105 parts of acetone are prepared into glue;
[0037] 4) Use 7628 glass cloth to impregnate the fabric glue, and bake it in an oven (oven temperature 175°C) for 2-8 minutes, remove the solvent to prepare ...
Embodiment 3
[0040] 1) Production of fabric glue: 60 parts of bisphenol A epoxy resin, 40 parts of o-cresol novolac epoxy resin, 2.8 parts of dicyandiamide, 15 parts of phenolic tripolyphosphazene, 35 parts of boehmite, 2 - 0.3 parts of ethyl-4 methylimidazole and 88 parts of DMF, prepared into glue;
[0041] 2) Preparation of glue A: 50 parts of water-soluble phenolic resin, 50 parts of phenoxytripolyphosphazene, 750 parts of acetone and 80 parts of water, prepared into glue;
[0042] 3) Production of glue B: 40 parts of bisphenol A epoxy resin, 20 parts of o-cresol novolac epoxy resin, 40 parts of phosphorus-containing epoxy resin, 35 parts of bisphenol F benzoxazine resin, tung oil modified phenolic resin 20 parts of resin, 30 parts of phenoxytripolyphosphazene, 70 parts of aluminum hydroxide, 0.2 parts of 2-ethyl-4 methylimidazole and 105 parts of acetone are prepared into glue;
[0043] 4) Use 7628 glass cloth to impregnate the fabric glue, and bake it in an oven (oven temperature 17...
PUM
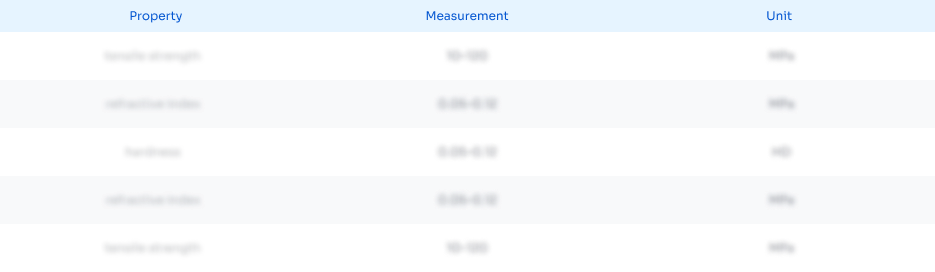
Abstract
Description
Claims
Application Information

- Generate Ideas
- Intellectual Property
- Life Sciences
- Materials
- Tech Scout
- Unparalleled Data Quality
- Higher Quality Content
- 60% Fewer Hallucinations
Browse by: Latest US Patents, China's latest patents, Technical Efficacy Thesaurus, Application Domain, Technology Topic, Popular Technical Reports.
© 2025 PatSnap. All rights reserved.Legal|Privacy policy|Modern Slavery Act Transparency Statement|Sitemap|About US| Contact US: help@patsnap.com