Annealing-free medium-high carbon steel plate making technology
A manufacturing process, medium and high carbon technology, applied in the field of steel rolling process, can solve the problems of reduced hardness of medium and high carbon steel plates, doubled production cycle, large wear of processing equipment, etc., to achieve the effect of increased elongation and high plasticity
- Summary
- Abstract
- Description
- Claims
- Application Information
AI Technical Summary
Problems solved by technology
Method used
Image
Examples
Embodiment 1
[0015] Example 1: The steel mill refines qualified molten steel and continuously casts into 72*1500mm slabs. The chemical composition is C: 0.48%, Si: 0.22%, Mn: 0.70%, P: 0.012%, S: 0.007%, Als: 0.020 %, the balance is Fe; the continuous casting billet is heated by a 230m tunnel heating furnace, the heating temperature is 1080 ℃, and the billet is rough-rolled and descaled after being discharged into the two rough rolling mills. The total rough rolling reduction rate is 65%. Intermediate cooling down to 830℃, after finishing rolling and descaling, it enters 5 finishing rolling mills for rolling. The thickness of the finished product is 5.0mm. After finishing rolling, it enters the laminar cooling section and the temperature is reduced to 680±20℃ for coiling. Pile cold. The chemical composition is listed in Table 1, the process parameters are listed in Table 2, and the mechanical properties and hardness of the finished product are listed in Table 3.
Embodiment 2
[0016] Example 2: The steel mill refines qualified molten steel and continuously casts into 72*1250mm slabs. The chemical composition is C: 0.49%, Si: 0.20%, Mn: 0.72%, P: 0.010%, S: 0.006%, Als: 0.022 %, the balance is Fe; the continuous casting billet is heated by a 230m tunnel heating furnace, the heating temperature is 1090℃, and the billet is rough-rolled and descaled after being discharged into the two rough rolling mills. The total rough rolling reduction rate is 65%. Intermediate cooling down to 840℃, after finishing rolling and descaling, it enters 5 finishing rolling mills for rolling. The thickness of the finished product is 5.0mm. After finishing rolling, it enters the laminar cooling section to cool down to 680±20℃ for coiling. Pile cold. The chemical composition is listed in Table 1, the process parameters are listed in Table 2, and the mechanical properties and hardness of the finished product are listed in Table 3.
Embodiment 3
[0017] Example 3: The steel mill refines qualified molten steel and continuously casts 72*1500mm slabs. The chemical composition is C: 0.51%, Si: 0.25%, Mn: 0.72%, P: 0.010%, S: 0.008%, Als: 0.024 %, the balance is Fe; the continuous casting billet is heated by a 230m tunnel heating furnace, the heating temperature is 1070℃, and the billet is rough-rolled and descaled after being discharged into the two roughing mills. The total roughing reduction rate is 65%. Intermediate cooling down to 810℃, after finishing rolling and descaling, it enters 5 finishing rolling mills for rolling. The thickness of the finished product is 4.5mm. After finishing rolling, it enters the laminar cooling section to cool down to 680±20℃ for coiling. Pile cold. The chemical composition is listed in Table 1, the process parameters are listed in Table 2, and the mechanical properties and hardness of the finished product are listed in Table 3.
[0018] Table 1
[0019]
[0020] Table 2
[0021]
[0022] tab...
PUM
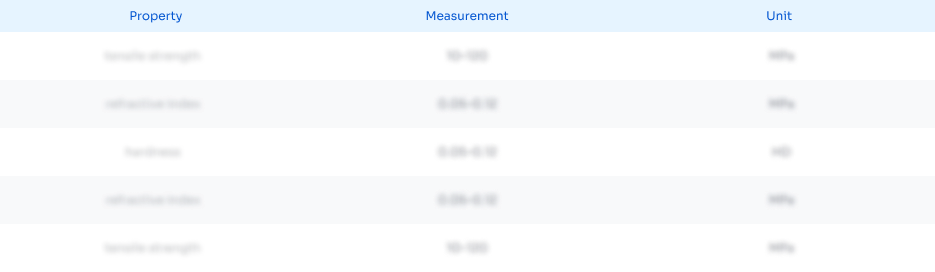
Abstract
Description
Claims
Application Information

- Generate Ideas
- Intellectual Property
- Life Sciences
- Materials
- Tech Scout
- Unparalleled Data Quality
- Higher Quality Content
- 60% Fewer Hallucinations
Browse by: Latest US Patents, China's latest patents, Technical Efficacy Thesaurus, Application Domain, Technology Topic, Popular Technical Reports.
© 2025 PatSnap. All rights reserved.Legal|Privacy policy|Modern Slavery Act Transparency Statement|Sitemap|About US| Contact US: help@patsnap.com