Method for producing hydration-resistant high-purity calcium oxide crucible
A calcium oxide crucible and hydration resistance technology, applied in the field of refractory materials for high temperature smelting, can solve the problems of smelting metals and alloys introducing impurities, short service life, easy hydration, etc., so as to reduce thermal shock resistance and improve resistance to The effect of improved hydration, hydration resistance and thermal shock resistance
- Summary
- Abstract
- Description
- Claims
- Application Information
AI Technical Summary
Problems solved by technology
Method used
Image
Examples
preparation example Construction
[0010] A preparation method of anti-hydration high-purity calcium oxide crucible adopts the following technical solutions:
[0011] a. The calcium carbonate with a purity greater than 98% is fused to obtain calcium oxide sand. After crushing, it is sieved and mixed evenly according to the following particle size and weight ratio:
[0012] <0.5mm 20-35%;
[0013] 0.5-1mm 15-25%;
[0014] 1-2mm 30-45%;
[0015] 2-4mm 5-10%.
[0016] b. Take the 92-98% graded calcium oxide sand and the zirconia powder with a particle size of 100-200μm and a mass ratio of 2-8% and mix well;
[0017] c. Add 3-10% anhydrous binder of the total weight of the above powder, wherein the anhydrous binder can be one or more of paraffin, ethanol, and 10% by weight calcium chloride ethanol solution; After being evenly mixed, pour it into a mold of corresponding size and place it on a vibrating table to vibrate; place the mold into cold isostatic pressing at a pressure of 180MPa-200MPa to form a calcium oxide crucible ...
Embodiment 1
[0020] The realization steps of the preparation method of the anti-hydration high-purity calcium oxide crucible:
[0021] a. The calcium carbonate with a purity greater than 98% is fused to obtain calcium oxide sand. After crushing, it is sieved and mixed evenly according to the following particle size and weight ratio:
[0022]
[0023] b. Take 96% graded calcium oxide sand and 4% zirconia powder with a particle size of 100-200μm and mix it evenly;
[0024] c. Add 6% paraffin wax based on the total weight of the powder. After mixing evenly, pour it into a mold of corresponding size, and place it on a vibrating table to vibrate. The mold is put into cold isostatic pressure and pressed to form a calcium oxide crucible body at a pressure of 180 MPa.
[0025] d. Heat the calcium oxide crucible body in a high temperature furnace at 15°C per minute to 500°C for 4 hours, then at 10°C per minute to 1200°C for 4 hours, and then at 10°C per minute to 1500°C for heat preservation 3 hours, and...
Embodiment 2
[0027] The realization steps of the preparation method of the anti-hydration high-purity calcium oxide crucible:
[0028] a. The calcium carbonate with a purity greater than 98% is fused to obtain calcium oxide sand. After crushing, it is sieved and mixed evenly according to the following particle size and weight ratio:
[0029]
[0030] b. Take 92% graded calcium oxide sand and 8% zirconia powder with a particle size of 100-200μm and mix well;
[0031] c. Add 8% ethanol of the total weight of the above powder. After evenly mixing, pour it into a mold of corresponding size, and place it on a vibrating table to vibrate. The mold is put into cold isostatic pressure and pressed at a pressure of 200 MPa to obtain a calcium oxide crucible body.
[0032] d. Heat the calcium oxide crucible body in a high temperature furnace at 15°C per minute to 450°C for 2 hours, then at 10°C per minute to 1100°C for 1 hour, and then at 10°C per minute to 1400°C for heat preservation 4 hours, and finally ...
PUM
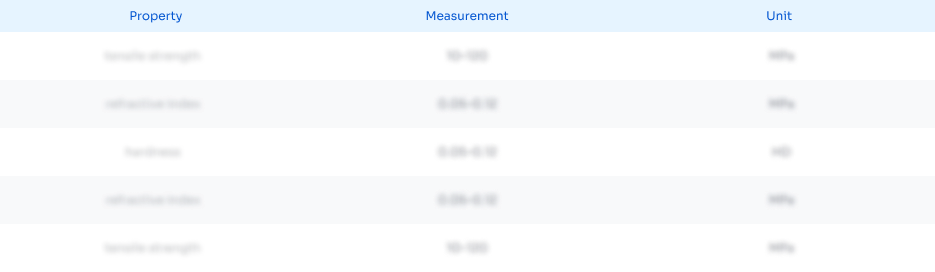
Abstract
Description
Claims
Application Information

- R&D
- Intellectual Property
- Life Sciences
- Materials
- Tech Scout
- Unparalleled Data Quality
- Higher Quality Content
- 60% Fewer Hallucinations
Browse by: Latest US Patents, China's latest patents, Technical Efficacy Thesaurus, Application Domain, Technology Topic, Popular Technical Reports.
© 2025 PatSnap. All rights reserved.Legal|Privacy policy|Modern Slavery Act Transparency Statement|Sitemap|About US| Contact US: help@patsnap.com