A method for preparing ferroniobium alloy by electrolysis of niobium concentrate molten oxide
A technology of molten oxide and niobium-iron alloy, which is applied in the fields of chemical instruments and methods, magnetic separation, solid separation, etc., can solve the problem that the resources of niobium in Baiyun Obo have not been effectively recycled, the process of hydrometallurgy is complicated, and the impurities do not meet the requirements of smelting. Steel requirements and other issues, to achieve the effect of green metallurgy, lower temperature, and low cost
- Summary
- Abstract
- Description
- Claims
- Application Information
AI Technical Summary
Problems solved by technology
Method used
Image
Examples
Embodiment 1
[0025] A method for preparing ferroniobium alloy by electrolysis of niobium concentrate molten oxide, the flow chart of which is as follows figure 1 As shown, the process and steps are as follows:
[0026] The composition of the niobium concentrate set in the present embodiment is roughly as follows: Nb 2 o 3 ≤5%, TFe≤45%, REO≤3%, CaO≤15%, Al 2 o 3 ≤10%, MgO≤5%, SiO 2 ≤15%, other ≤5%;
[0027] Selective reduction and magnetic separation of niobium concentrate: using H 2 The gas reducing agent reduces the iron oxides in the solid niobium concentrate powder at 1200°C, the reduction time is 0.5 hours, the reduced mixture is pulverized, and separated by magnetic separation to obtain pure iron powder and rich niobium and rare earth A mixture wherein the niobium-iron ratio in the niobium-rich and rare earth mixture is 0.15;
[0028] Preparation of niobium-iron alloy by molten salt electrolysis: Melt niobium-rich and rare earth mixture at 1550°C, use high-melting-point Pt meta...
Embodiment 2
[0030] Selective reduction and magnetic separation of niobium concentrate: Use CO gas reducing agent to reduce the iron oxide in solid niobium concentrate powder at 1000°C, the reduction time is 1 hour, pulverize the reduced mixture, and use magnetic separation separation method to obtain pure iron powder and niobium-rich and rare earth mixture, wherein the niobium-iron ratio in the niobium-rich and rare earth mixture is 0.25;
[0031] Preparation of niobium-iron alloy by molten salt electrolysis: at 1450°C, melt the niobium-rich and rare earth mixture, use a high melting point Ir metal electrode, and apply a voltage between the two electrodes in the molten oxide electrolyte for 4 hours; the electrolysis method is pulse current electrolysis , the peak voltage range is 3.5V, the duty cycle is 10.0, and the pulse frequency is 500Hz; CaO and Al are added during electrolysis 2 o 3 Reagents to adjust the molten oxide composition to maintain the mass percentage of CaO in the molten...
Embodiment 3
[0033] Selective reduction and magnetic separation of niobium concentrate: using CO gas with a gas volume of 50% and H with a gas volume of 50% 2 The gas mixed gas reducing agent reduces the iron oxides in the solid niobium concentrate powder at 1000°C, the reduction time is 1.5 hours, the reduced mixture is pulverized, and separated by magnetic separation to obtain pure iron powder and rich Niobium and rare earth mixture, wherein the niobium-iron ratio in the niobium-rich and rare earth mixture is 0.95;
[0034] Preparation of niobium-iron alloy by molten salt electrolysis: Melt niobium-rich and rare earth mixture at 1550°C, use a high-melting point Ir metal electrode, and apply a voltage between the two electrodes in the molten oxide electrolyte for 4 hours; the electrolysis method is constant voltage electrolysis , the voltage range is 3.5V; CaO and Al are added during electrolysis 2 o 3 Reagents to adjust the molten oxide composition to maintain the mass percentage of Ca...
PUM
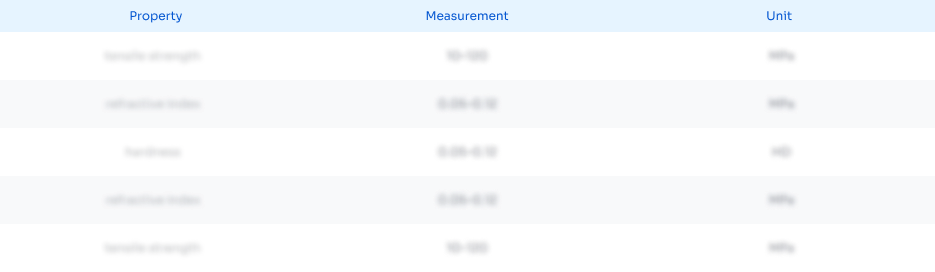
Abstract
Description
Claims
Application Information

- R&D Engineer
- R&D Manager
- IP Professional
- Industry Leading Data Capabilities
- Powerful AI technology
- Patent DNA Extraction
Browse by: Latest US Patents, China's latest patents, Technical Efficacy Thesaurus, Application Domain, Technology Topic, Popular Technical Reports.
© 2024 PatSnap. All rights reserved.Legal|Privacy policy|Modern Slavery Act Transparency Statement|Sitemap|About US| Contact US: help@patsnap.com