Method for manufacturing honeycomb core with filling material by using textile waste
A technology for textile waste and filling materials, applied in chemical instruments and methods, lamination auxiliary operations, lamination devices, etc., can solve the problems of poor sound insulation performance, honeycomb panels can not meet the needs of modern engineering, poor thermal insulation performance, etc., to improve Mechanical properties, improved thermal and acoustic insulation, cost reduction effects
- Summary
- Abstract
- Description
- Claims
- Application Information
AI Technical Summary
Problems solved by technology
Method used
Image
Examples
Embodiment Construction
[0017] The present invention will be described below in conjunction with specific embodiments.
[0018] This embodiment relates to a specific method for making a honeycomb core with filling material from textile waste, including the following process steps:
[0019] (1) Textile waste treatment and production of reprocessed fiber felt
[0020] Because it is necessary to prepare two fiber mats with different thermal properties, one containing thermoplastic fibers and the other without thermoplastic fibers, the treatment of textile waste is divided into two processes. Preparation of fiber mats containing thermoplastic fibers: Textile waste is mainly made of ordinary garment waste and polypropylene waste silk, polypropylene waste silk is used as binder fiber, ordinary garment leftover waste is the main fiber, and the content of polypropylene waste silk is 50%. Considering the different sizes and lengths of the raw materials, especially the polypropylene waste yarn is not easy to ...
PUM
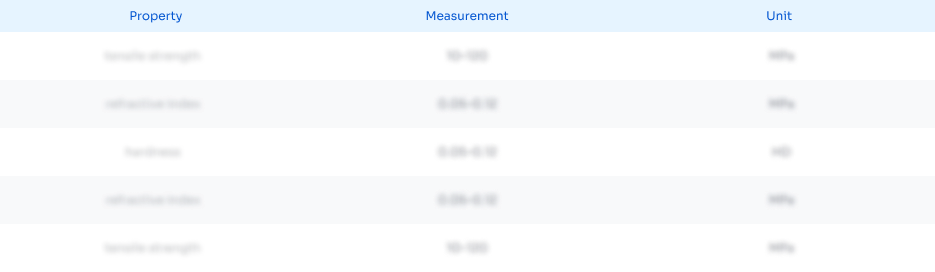
Abstract
Description
Claims
Application Information

- R&D
- Intellectual Property
- Life Sciences
- Materials
- Tech Scout
- Unparalleled Data Quality
- Higher Quality Content
- 60% Fewer Hallucinations
Browse by: Latest US Patents, China's latest patents, Technical Efficacy Thesaurus, Application Domain, Technology Topic, Popular Technical Reports.
© 2025 PatSnap. All rights reserved.Legal|Privacy policy|Modern Slavery Act Transparency Statement|Sitemap|About US| Contact US: help@patsnap.com