Centrifugal casting method of chromium-containing high silicon cast iron anode tube
A high-silicon cast iron and centrifugal casting technology, which is applied in the production of cathodic protection materials for underground steel facilities, can solve problems such as poor product performance and uneven wall thickness, and achieve the effects of no pores, high yield, and improved internal structure.
- Summary
- Abstract
- Description
- Claims
- Application Information
AI Technical Summary
Problems solved by technology
Method used
Examples
Embodiment 1
[0014] Example 1, Get 142 kilograms of silicon, 32.5 kilograms of chromium, 7 kilograms of carbon, 1 kilogram of copper, 817.5 kilograms of iron, and 1000 kilograms of ingredients;
[0015] For smelting, the raw materials are added to the smelting furnace for smelting for 60 minutes, and when the temperature of the melt reaches 1400 degrees Celsius, it is transferred to the refining furnace;
[0016] Refining, when the refining furnace reaches 1420 degrees Celsius, add 0.3% rare earth silicon alloy as raw material, and the temperature rises to 1450 degrees Celsius for pouring;
[0017] For pouring, control the speed of the centrifuge at 1800--2500 rpm. After the pouring and feeding are completed, the centrifuge will continue to stop for 1 minute;
[0018] The mold is released, and the casting is cooled to 1000 degrees Celsius to release the mold;
[0019] Heat preservation and tempering, put the castings out of the mold into the heat preservation furnace, control the furnace...
Embodiment 2
[0020] Example 2, Prepare 295 kg of silicon, 100 kg of chromium, 22 kg of carbon, 10 kg of copper, 1573 kg of iron, and 2000 kg of ingredients;
[0021] For smelting, put the raw materials into the smelting furnace and smelt for 50 minutes, and transfer to the refining furnace when the temperature of the melt reaches 1400 degrees Celsius;
[0022] Refining, when the refining furnace reaches 1420 degrees Celsius, add 0.3% rare earth silicon alloy as raw material, and the temperature rises to 1450 degrees Celsius for pouring;
[0023] For pouring, control the speed of the centrifuge at 1800--2500 rpm. After the pouring and feeding are completed, the centrifuge will continue to stop for 1 minute;
[0024] Release the mold, and the casting is cooled to 1050 degrees Celsius to release the mold;
[0025] Heat preservation and tempering, put the castings out of the mold into the heat preservation furnace, control the temperature of the furnace at 1000-1020 degrees Celsius, keep th...
Embodiment 3
[0026] Example 3, Get 435 kg of silicon, 120 kg of chromium, 27 kg of carbon, 9 kg of copper, 2409 kg of iron, and 3000 kg of ingredients;
[0027] For smelting, the raw materials are added to the smelting furnace for smelting for 55 minutes, and when the temperature of the melt reaches 1400 degrees Celsius, it is transferred to the refining furnace;
[0028] Refining, when the refining furnace reaches 1420 degrees Celsius, add 0.3% of the raw material rare earth silicon alloy, and the temperature rises to 1430 degrees Celsius for pouring;
[0029] For pouring, control the speed of the centrifuge at 1800--2500 rpm. After the pouring and feeding are completed, the centrifuge will continue to stop for 1 minute;
[0030] The mold is released, and the casting is cooled to 1000 degrees Celsius to release the mold;
[0031] Heat preservation and tempering, put the castings out of the mold into the heat preservation furnace, control the temperature of the furnace at 1000-1020 degr...
PUM
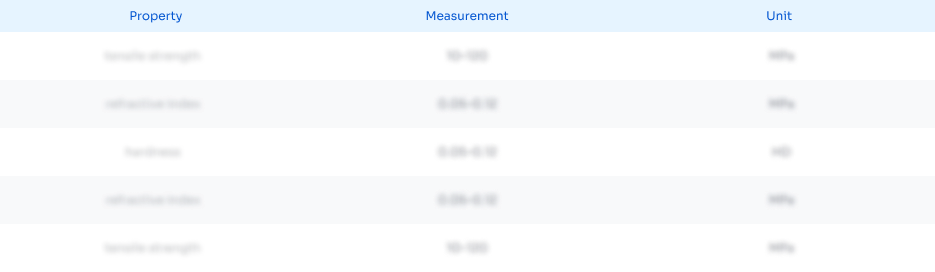
Abstract
Description
Claims
Application Information

- R&D
- Intellectual Property
- Life Sciences
- Materials
- Tech Scout
- Unparalleled Data Quality
- Higher Quality Content
- 60% Fewer Hallucinations
Browse by: Latest US Patents, China's latest patents, Technical Efficacy Thesaurus, Application Domain, Technology Topic, Popular Technical Reports.
© 2025 PatSnap. All rights reserved.Legal|Privacy policy|Modern Slavery Act Transparency Statement|Sitemap|About US| Contact US: help@patsnap.com