Converter steelmaking phosphorus reservation smelting method
A smelting method and converter steelmaking technology, applied in the field of metallurgy, can solve the problems of increased consumption of iron and steel materials, production accidents of large and medium-sized converters, and rising costs, and achieve the effects of increasing residual manganese content, reducing smelting costs, and increasing the amount of tapped steel.
- Summary
- Abstract
- Description
- Claims
- Application Information
AI Technical Summary
Problems solved by technology
Method used
Image
Examples
Embodiment
[0019] A large amount of test data (wherein TFe% represents the content of iron oxide, m 3 / t.min is cubic meter / ton of steel. per minute) based on analysis and optimization induction.
[0020] The verification shows that controlling the binary basicity R of the slag, the content of magnesium oxide in the slag, and controlling the main composition of the slag by controlling the oxidizability of the slag during the smelting process (TFe% content) all help to increase the phosphorus content and molten steel at the end of the converter. residual manganese content. The process oxidation of slag can be effectively controlled by controlling the appropriate oxygen supply intensity, the impact depth of the oxygen jet and the time for maintaining the depth. Usually, the composition control range of the main components of slag is as follows:
[0021] TFe%
CaO%
SiO 2 %
CaO / SiO 2
MgO%
≤15%
35~50%
10~25%
2.0~2.8
10~18%
...
PUM
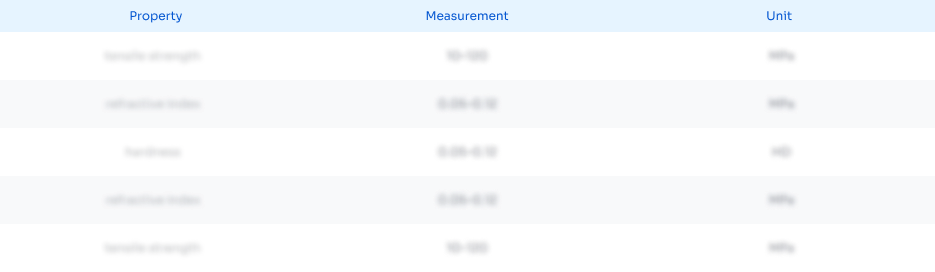
Abstract
Description
Claims
Application Information

- Generate Ideas
- Intellectual Property
- Life Sciences
- Materials
- Tech Scout
- Unparalleled Data Quality
- Higher Quality Content
- 60% Fewer Hallucinations
Browse by: Latest US Patents, China's latest patents, Technical Efficacy Thesaurus, Application Domain, Technology Topic, Popular Technical Reports.
© 2025 PatSnap. All rights reserved.Legal|Privacy policy|Modern Slavery Act Transparency Statement|Sitemap|About US| Contact US: help@patsnap.com