Poly ethylene (PE) combined pipe
A composite pipe and layer composite technology, applied in the field of composite pipes, can solve the problems of easy leakage, affect the firmness of the pipes, and high production costs, and achieve the effects of increasing compressive strength, high bonding strength and long service life.
- Summary
- Abstract
- Description
- Claims
- Application Information
AI Technical Summary
Problems solved by technology
Method used
Image
Examples
Embodiment 1
[0017] Embodiment 1: Put 50 parts of HDPE resin (high-density polyethylene), 0.2 part of sorbitol, and 5 parts of thermoplastic polyurethane elastomer into the hopper of the first extruder by weight; 80 parts of HDPE resin, calcium carbonate 5 parts by weight 1 part of calcium stearate, 2 parts of nano-sized titanium dioxide, 0.3 part of tetrakis[β-(3,5-di-tert-butyl-4-hydroxyphenyl) propionate] pentaerythritol ester, 0.3 part of phenyl o-hydroxybenzoate 0.2 part of polyethylene wax and 0.2 part of polyethylene wax are mixed and put into the hopper of the second extruder; the third extruder prepares the HDPE core pipe 5. During production, the HDPE core tube 5 is extruded by the third extruder. After water cooling and sizing, the stainless steel wire is wound on the HDPE core tube 5 in a left-handed and right-handed manner from the left and right sides, and the winding angle is 50 degrees. , so that the pipe is evenly stressed in the axial and circumferential directions to for...
Embodiment 2
[0018] Embodiment 2: Put 50 parts of HDPE resin (high-density polyethylene), 0.5 part of sorbitol, and 5 parts of thermoplastic polyurethane elastomer into the hopper of the first extruder by weight; 83 parts of HDPE resin, 8 parts of calcium carbonate by weight 3 parts of calcium stearate, 2 parts of nano-sized titanium dioxide, 0.4 parts of tetrakis[β-(3,5-di-tert-butyl-4-hydroxyphenyl) propionate] pentaerythritol ester, 0.4 parts of phenyl o-hydroxybenzoate 0.2 part of polyethylene wax and 0.2 part of polyethylene wax are mixed and put into the hopper of the second extruder; the third extruder prepares the HDPE core pipe 5. The production method is the same as above.
Embodiment 3
[0019] Embodiment 3: Put 50 parts of HDPE resin (high-density polyethylene), 1.1 parts of sorbitol, and 5 parts of thermoplastic polyurethane elastomer into the hopper of the first extruder by weight; 85 parts of HDPE resin, 10 parts of calcium carbonate by weight 5 parts of calcium stearate, 3 parts of nano-sized titanium dioxide, 0.5 parts of pentaerythritol tetrakis[β-(3,5-di-tert-butyl-4-hydroxyphenyl) propionate, 0.5 parts of phenyl o-hydroxybenzoate 0.3 parts of polyethylene wax and 0.3 parts of polyethylene wax are mixed and put into the hopper of the second extruder; the third extruder prepares HDPE core pipe 5. The production method is the same as above.
PUM
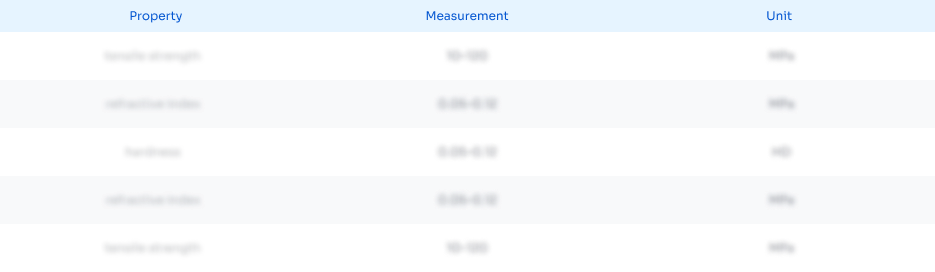
Abstract
Description
Claims
Application Information

- R&D
- Intellectual Property
- Life Sciences
- Materials
- Tech Scout
- Unparalleled Data Quality
- Higher Quality Content
- 60% Fewer Hallucinations
Browse by: Latest US Patents, China's latest patents, Technical Efficacy Thesaurus, Application Domain, Technology Topic, Popular Technical Reports.
© 2025 PatSnap. All rights reserved.Legal|Privacy policy|Modern Slavery Act Transparency Statement|Sitemap|About US| Contact US: help@patsnap.com