Nickel-base amorphous alloy powder as well as nickel-base amorphous composite coating and preparation method thereof
A technology of amorphous alloy and amorphous powder, which is applied in the field of surface coating, can solve the problems of low amorphous content of coating, reduction of amorphous content of coating, burning loss, etc., and achieve high amorphous volume content and microhardness , strong amorphous forming ability, and wide application range
- Summary
- Abstract
- Description
- Claims
- Application Information
AI Technical Summary
Problems solved by technology
Method used
Image
Examples
Embodiment 1
[0031] Example 1, the selected powder composition is (by weight percentage): 32.4%Fe, 4.4%B, 6.3%Si, 8.2%Nb, and the balance is Ni. The macroscopic appearance and X-ray diffraction of the powder obtained after atomization Spectrum such as figure 1 and figure 2 shown by figure 1 It can be seen that the particle size of the obtained powder is relatively uniform, and most of them are spherical, which can ensure the fluidity of the laser cladding powder feeding, and the strength of the powder is 100 mesh to 350 mesh. The XRD pattern of the powder ( figure 2 ) is mainly manifested as a diffuse scattering peak, so it is considered that the powder is mainly composed of amorphous phase, with only a small amount of crystalline phase, and the calculated amount of crystalline phase is about 5%. On the one hand, this shows that the alloy system given in this study has a high ability to form amorphous; on the other hand, it shows that the composition of the powder is very close to the...
Embodiment 2
[0034] Example 2, the selected powder components are (by weight percentage): 30.4% Fe, 3.6% B, 5.2% Si, 7% Nb, and the balance is Ni. The particle size of the obtained powder after atomization is 100~350 mesh. First, semiconductor laser cladding is used to prepare nickel-based alloy laser cladding coating on the surface of low carbon steel, and then laser rapid remelting is performed on the coating surface. Laser cladding parameters are: laser power 700W, laser scanning speed 0.36m / min, powder feeding volume 12g / min, protective gas flow 15L / min. The parameters during laser remelting are: laser power is 3500W, laser scanning speed is 8m / min during remelting, and protective gas flow rate is 15L / min.
[0035] Figure 5 This is the scanning electron micrograph of the microstructure of the obtained laser remelted layer, which shows the microscopic appearance of many white granular phases distributed on the matrix without obvious grain boundaries. The matrix is a typical feature...
Embodiment 3
[0036] Example 3, the selected powder components are (by weight percentage): 32.4% Fe, 4.4% B, 6.3% Si, 8.2% Nb, and the balance is Ni. The particle size of the obtained powder after atomization is 100~350 mesh. First, semiconductor laser cladding is used to prepare nickel-based alloy laser cladding coating on the surface of low carbon steel, and then laser rapid remelting is performed on the coating surface. Laser cladding parameters are: laser power 700W, laser scanning speed 0.36m / min, powder feeding volume 12g / min, protective gas flow 15L / min. The parameters during laser remelting are: laser power is 3500W, laser scanning speed is 7m / min during remelting, and protective gas flow rate is 15L / min.
[0037] Figure 7 The scanning electron micrograph of the microstructure of the obtained laser remelting layer shows that the obtained coating is very dense and has no defects such as cracks and pores. The microstructure shows that there are many white granular phases distribut...
PUM
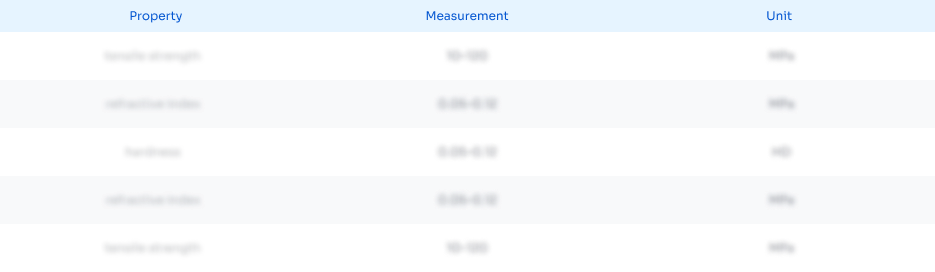
Abstract
Description
Claims
Application Information

- R&D
- Intellectual Property
- Life Sciences
- Materials
- Tech Scout
- Unparalleled Data Quality
- Higher Quality Content
- 60% Fewer Hallucinations
Browse by: Latest US Patents, China's latest patents, Technical Efficacy Thesaurus, Application Domain, Technology Topic, Popular Technical Reports.
© 2025 PatSnap. All rights reserved.Legal|Privacy policy|Modern Slavery Act Transparency Statement|Sitemap|About US| Contact US: help@patsnap.com