A micro-nano composite porous copper surface structure and its preparation method and device
A technology of surface structure and porous copper, applied in the direction of nanotechnology, nanotechnology, nanotechnology for materials and surface science, etc., can solve the problems of high cost, poor controllability, complex process, etc., to achieve enhanced mechanical properties, The effect of preventing mutual interference
- Summary
- Abstract
- Description
- Claims
- Application Information
AI Technical Summary
Problems solved by technology
Method used
Image
Examples
Embodiment 1
[0031] An electrodeposition device for preparing a micro-nano composite porous copper surface structure such as figure 1 As shown, it includes an electrodeposition tank 1, an electrodeposition solution 2, a DC power supply 3, a cathode substrate 4 and an anode 5, the anode 5 and the cathode substrate 4 are respectively connected to the positive and negative poles of the DC power supply 3, the electrodeposition solution 2, the cathode substrate 4 and the anode 5 are placed in the electrodeposition tank 1, and the electrodeposition liquid 2 is immersed in the cathode substrate 4 and the anode 5.
[0032] The cathode base 4 and the anode 5 are copper columns and copper plates respectively. The cathode base 4 is placed at the bottom of the electrodeposition tank 1 . Both the cathode base 4 and the anode 5 are placed horizontally, so that the hydrogen bubbles on the surface of the cathode base are evenly distributed and separated, and mutual interference is prevented; the area of ...
Embodiment 2
[0034] (1) Prepare electrodeposition solution. Electrodeposition solution 2 composition: CuSO 4 Concentration is 0.4mol / L, H 2 SO 4 The concentration is 1.5mol / L, and the additive is HCl and the concentration is 20mmol / L.
[0035] (2) Prepare the cathode substrate. The cathode substrate 4 is made of copper pillars, and the electrodeposition is only carried out on the dome surface. The dome surface is polished with 800-1000 mesh sandpaper, and methanol / nitric acid (V / V)=9 / 1 is used as the polishing liquid, and the voltage is 6-7V / cm 2 Perform electrolytic polishing and activate with 10wt% dilute sulfuric acid; coat the surface of the cathode substrate 4 that is not subjected to electrodeposition with silica gel 704.
[0036] (3) Prepare the anode. The anode 5 is made of red copper plate, and the area of the anode should be large enough to obtain a uniform current density for the cathode substrate.
[0037] (4) Connection device. Press the device figure 1 connect.
[...
PUM
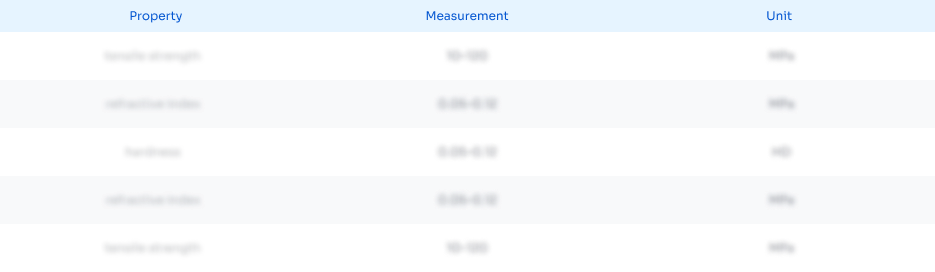
Abstract
Description
Claims
Application Information

- R&D Engineer
- R&D Manager
- IP Professional
- Industry Leading Data Capabilities
- Powerful AI technology
- Patent DNA Extraction
Browse by: Latest US Patents, China's latest patents, Technical Efficacy Thesaurus, Application Domain, Technology Topic, Popular Technical Reports.
© 2024 PatSnap. All rights reserved.Legal|Privacy policy|Modern Slavery Act Transparency Statement|Sitemap|About US| Contact US: help@patsnap.com