A kind of preparation method containing dianhydrosugar alcohol copolyester
A technology of dianhydrohexitol and polyester, applied in the direction of single-component copolyester rayon, etc., can solve the problems of catalyst sensitivity, low hydroxyl reactivity, and difficulty in obtaining high-molecular copolyester, and achieve Enhanced reactivity, shortened polycondensation reaction time, and better hue of reactants
- Summary
- Abstract
- Description
- Claims
- Application Information
AI Technical Summary
Problems solved by technology
Method used
Image
Examples
Embodiment 1
[0040] Put terephthalic acid and ethylene glycol with a molar ratio of 1:1.1, the catalyst antimony acetate and the stabilizer triphenyl phosphite into the mixing device, mix them and add them to the esterification reactor for esterification reaction, the esterification rate After reaching more than 90%, isosorbide dissolved in ethylene glycol is added to the system, the pH value is 8, and the content of isosorbide accounts for 3% of the total amount of terephthalic acid. After uniform mixing, a precondensation reaction is carried out, the reaction temperature is 255° C., the pressure is 900 Pa, and the reaction time is 50 minutes. After the pre-polycondensation reaction, the final polycondensation reaction is carried out. The reaction temperature is 285°C and the pressure is 100Pa. When the melt dynamic viscosity meets the requirements, the material is discharged, extruded, and pelletized. The intrinsic viscosity is 0.6dl / g.
Embodiment 2
[0042] Put terephthalic acid and ethylene glycol with a molar ratio of 1:1.1, the catalyst antimony acetate and the stabilizer triphenyl phosphite into the mixing device, and after mixing, put them into the esterification reactor for esterification reaction, and the esterification rate reaches When it is above 90%, add isosorbide dissolved in ethylene glycol to the system, the content of isosorbide accounts for 10% of the total moles of terephthalic acid, and its pH value is 8. After uniform mixing, a precondensation reaction is carried out, the reaction temperature is 255° C., the pressure is 900 Pa, and the reaction time is 50 minutes. After the pre-polycondensation reaction, the final polycondensation reaction is carried out. The reaction temperature is 290°C and the pressure is 100Pa. When the melt dynamic viscosity meets the requirements, the material is discharged, extruded, and pelletized. The intrinsic viscosity is 0.6dl / g.
Embodiment 3
[0044] Put terephthalic acid and ethylene glycol with a molar ratio of 1:1.1, the catalyst antimony acetate and the stabilizer triphenyl phosphite into the mixing device, and after mixing, put them into the esterification reactor for esterification reaction, and the esterification rate reaches When it is above 90%, add isosorbide dissolved in ethylene glycol to the system, the content of isosorbide accounts for 10% of the total moles of terephthalic acid, and its pH value is 8. After uniform mixing, a precondensation reaction is carried out, the reaction temperature is 255° C., the pressure is 900 Pa, and the reaction time is 50 minutes. After the pre-polycondensation reaction, the final polycondensation reaction is carried out. The reaction temperature is 290°C and the pressure is 100Pa. When the melt dynamic viscosity meets the requirements, the material is discharged, extruded, and pelletized. The intrinsic viscosity is 0.75dl / g.
PUM
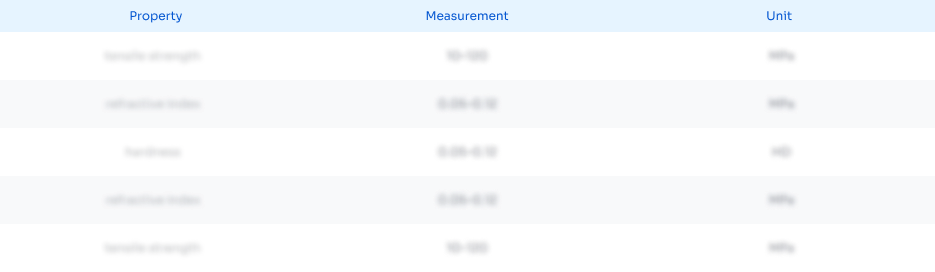
Abstract
Description
Claims
Application Information

- R&D
- Intellectual Property
- Life Sciences
- Materials
- Tech Scout
- Unparalleled Data Quality
- Higher Quality Content
- 60% Fewer Hallucinations
Browse by: Latest US Patents, China's latest patents, Technical Efficacy Thesaurus, Application Domain, Technology Topic, Popular Technical Reports.
© 2025 PatSnap. All rights reserved.Legal|Privacy policy|Modern Slavery Act Transparency Statement|Sitemap|About US| Contact US: help@patsnap.com