Synchronous coloring burn-out printing and moire infiltrating burn-out printing technique for denim fabrics
A printing process, denim technology, applied in the direction of dyeing method, biochemical fiber treatment, fiber type, etc., can solve the problems of thick and hot denim, poor air permeability, poor color fastness, etc., to achieve perfect style characteristics, reduce Labor, the effect of reducing production costs
- Summary
- Abstract
- Description
- Claims
- Application Information
AI Technical Summary
Problems solved by technology
Method used
Examples
Embodiment 1
[0016] This example adopts cotton-polyester denim gray fabric, and its process steps are as follows: firstly, carry out rotten printing pretreatment, that is, the cotton-polyester denim gray fabric is desizing treated with amylase at 40°C, and then screen plate-making to make different styles of synchronous Coloring the printing screen or moire to penetrate the printing screen, and configuring the printing paste; secondly, use the prepared printing paste to infiltrate the printing screen by synchronously coloring the printing screen or clouding on the denim gray fabric The plate is processed with simultaneous coloring and printing, and cloud pattern infiltration printing. The processing flow is as follows: color matching→cloth patching→printing and squeegee→drying and drying cloth→baking and carbonization→finished product.
[0017] Simultaneous coloring printing screen plate adopts 80 purpose plate making, and moiré penetration printing screen plate adopts 140 purpose plate mak...
Embodiment 2
[0022] This example adopts cotton-polyester elastic denim gray cloth, and its process steps are as follows: firstly, carry out rotten printing pretreatment, that is, desizing denim gray cloth at 60°C with amylase, and then screen plate-making to make different styles of simultaneous coloring The bad printing screen or moiré penetrates the bad printing screen, and configures the bad printing paste; secondly, uses the prepared bad printing paste to infiltrate the bad printing screen or moiré on the denim fabric by synchronously coloring the bad printing screen Simultaneous coloring printing and moiré penetration printing processing are carried out. The processing flow is as follows: color matching→cloth patching→printing squeegee→drying cloth→baking and carbonization→finished product.
[0023] Simultaneous coloring printing screen plate adopts 100-mesh plate making, and moiré penetration printing screen plate adopts 200-mesh plate making. In the simultaneous coloring and rotten ...
PUM
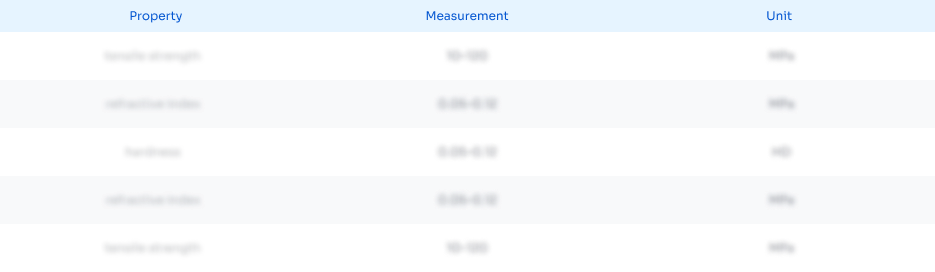
Abstract
Description
Claims
Application Information

- R&D
- Intellectual Property
- Life Sciences
- Materials
- Tech Scout
- Unparalleled Data Quality
- Higher Quality Content
- 60% Fewer Hallucinations
Browse by: Latest US Patents, China's latest patents, Technical Efficacy Thesaurus, Application Domain, Technology Topic, Popular Technical Reports.
© 2025 PatSnap. All rights reserved.Legal|Privacy policy|Modern Slavery Act Transparency Statement|Sitemap|About US| Contact US: help@patsnap.com