Method for preparing hot pressed sintered high-density magnesium oxide target
A hot-pressing sintering and magnesia technology, which is applied in the preparation of hot-pressing sintered high-density magnesia targets and the preparation of magnesia targets, can solve the problems of target deformation, low target purity, and low yield. , to achieve the effect of not easy to deform and crack, simple preparation process and high yield
- Summary
- Abstract
- Description
- Claims
- Application Information
AI Technical Summary
Problems solved by technology
Method used
Examples
Embodiment 1
[0006] Embodiment 1: Weigh a certain amount of high-purity nano-magnesia powder with an average particle diameter of 50 nm and a purity of ≥99.99%. Select the diameter of the target prepared according to the requirements and select the mold with the same diameter, put the mold into the hot-press sintering furnace, and gradually load the raw materials into the mold by moving the vibrating funnel evenly and reciprocatingly, the purpose is to make the powder accumulate evenly in the mold, And measure the material height of a group of point powder in the mold, the height difference of each point is less than 0.5mm. The furnace is evacuated, and when the vacuum is 150MPa, turn on the power and start heating. When the temperature reaches 900°C, start to pressurize until the temperature reaches 1450°C. The pressurization rate was 1 MPa / min. When the pressure reaches 50MPa, keep the pressure for 50 minutes. When the pressure head on the press reaches the specified displacement, turn...
Embodiment 2
[0007] Embodiment 2: weighing a certain amount of high-purity nano-magnesia powder with an average particle diameter of 70nm and a purity of ≥99.99%. Select the diameter of the target prepared according to the requirements and select the mold with the same diameter, put the mold into the hot pressing sintering furnace, and gradually load the raw materials into the mold by moving the vibrating funnel evenly and reciprocatingly, the purpose is to make the powder accumulate evenly in the mold, And measure the material height of a group of point powder in the mold, the height difference of each point is less than 0.5mm. The furnace is evacuated, and when the vacuum is 200MPa, turn on the power and start heating. When the temperature reaches 900°C, start to pressurize until the temperature reaches 1500°C, and the pressurization rate is 1MPa / min. When the pressure reaches 40MPa, keep the pressure for 40 minutes. When the pressure head on the press reaches the specified displacement...
Embodiment 3
[0008] Embodiment 3: Weigh a certain amount of high-purity nano-magnesia powder with an average particle diameter of 60 nm and a purity of ≥99.99%. Select the diameter of the target prepared according to the requirements and select the mold with the same diameter, put the mold into the hot pressing sintering furnace, and gradually load the raw materials into the mold by moving the vibrating funnel evenly and reciprocatingly, the purpose is to make the powder accumulate evenly in the mold, And measure the material height of a group of point powder in the mold, the height difference of each point is less than 0.5mm. The furnace is evacuated, and when the vacuum is 400MPa, turn on the power and start heating. When the temperature reaches 900°C, start to pressurize until the temperature reaches 1500°C, and the pressurization rate is 1MPa / min. When the pressure reaches 20MPa, keep the pressure for 50 minutes. When the pressure head on the press reaches the specified displacement, ...
PUM
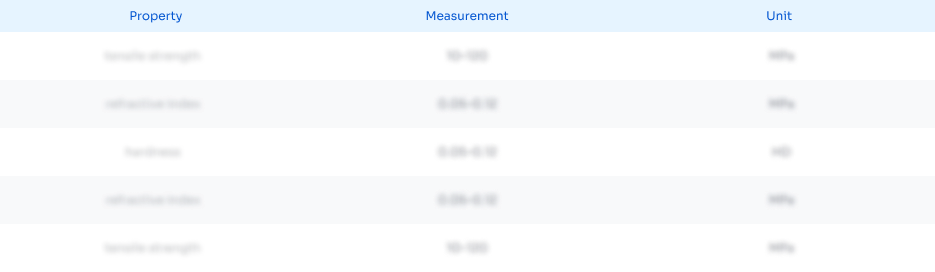
Abstract
Description
Claims
Application Information

- R&D
- Intellectual Property
- Life Sciences
- Materials
- Tech Scout
- Unparalleled Data Quality
- Higher Quality Content
- 60% Fewer Hallucinations
Browse by: Latest US Patents, China's latest patents, Technical Efficacy Thesaurus, Application Domain, Technology Topic, Popular Technical Reports.
© 2025 PatSnap. All rights reserved.Legal|Privacy policy|Modern Slavery Act Transparency Statement|Sitemap|About US| Contact US: help@patsnap.com