Deep diffusion process for manufacturing diodes
A deep diffusion and diode technology, applied in the field of deep diffusion process, can solve the problems of difficult handling, affecting electrical properties, complicated and tedious processes, etc., and achieve the effects of saving power costs, saving labor costs, and improving performance
- Summary
- Abstract
- Description
- Claims
- Application Information
AI Technical Summary
Problems solved by technology
Method used
Examples
Embodiment Construction
[0008] Concrete steps of the present invention are as follows:
[0009] First, clean the original silicon wafer: place the silicon wafer in mixed acid for 60 seconds, rinse with pure water for 5-10 minutes, then put it into hydrofluoric acid for 5±0.1 minutes, then rinse with pure water at room temperature for 5-10 minutes, then put The silicon wafer is placed in the Harmo powder solution, cleaned with an ultrasonic wave with a frequency of 2.8KHZ for 20±1min, followed by routine rinsing with pure water, then ultrasonically cleaned with hot pure water for 20±1min, and finally rinsed with pure water for 5-10min, and the cleaning is completed. , dehydration is carried out twice with room temperature IPA solution, each dehydration time is 2±0.1 min, and this process is completed.
[0010] The second step, phosphor paper: take out a piece of phosphor paper with tweezers and place it between the first and second silicon wafers on either side of the flower basket, and so on. Place ...
PUM
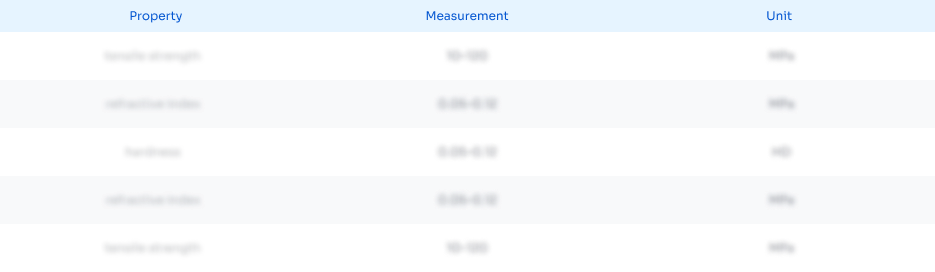
Abstract
Description
Claims
Application Information

- R&D
- Intellectual Property
- Life Sciences
- Materials
- Tech Scout
- Unparalleled Data Quality
- Higher Quality Content
- 60% Fewer Hallucinations
Browse by: Latest US Patents, China's latest patents, Technical Efficacy Thesaurus, Application Domain, Technology Topic, Popular Technical Reports.
© 2025 PatSnap. All rights reserved.Legal|Privacy policy|Modern Slavery Act Transparency Statement|Sitemap|About US| Contact US: help@patsnap.com