Efficient preparation method for nanostructure oxide dispersion strengthening steel
A technology of dispersion strengthening and nanostructure, which is applied in the field of efficient preparation of nanostructured oxide dispersion strengthened steel, can solve the problems that affect the successful preparation of nanostructured oxide dispersion strengthened steel, performance deterioration, low efficiency, etc., and achieve the suppression of non-nanostructure and the formation of harmful precipitated phases, improving the overall performance and reducing the cost of preparation
- Summary
- Abstract
- Description
- Claims
- Application Information
AI Technical Summary
Problems solved by technology
Method used
Examples
Embodiment 1
[0028] Preparation of nanostructured oxide dispersion strengthened martensitic steel, the alloy composition is (the number before the alloy element is the mass percentage, the same below) Fe-9Cr-1W-0.3Ti-0.3Y-0.1Al-0.2OTa.
[0029] According to the mass ratio, the alloy constituent elements other than Y and Ti are used as raw materials, put into the induction furnace of the atomization equipment, and evacuated to a vacuum degree of 8.8×10 -2 Pa, then filled with ultra-high purity H with a purity of 99.9999% 2 to 0.03MPa, heat and turn on the electromagnetic stirring until the alloy raw materials are completely melted, then add Y and Ti to the melt, and then evacuate to 9.3×10 -2 Pa, followed by atomization and pulverization. Argon is used as the atomizing gas, the atomizing pressure is 6.1 MPa, the flow rate of the alloy liquid is 0.3 kg / s, and the average particle size of the atomized alloy powder is ~110 μm. The atomized alloy powder is detected by X-diffraction, showing o...
Embodiment 2
[0031] The nanostructured oxide dispersion strengthened martensitic steel was prepared, and the alloy composition was Fe-8Cr-2W-0.9Ti-0.4Y-0.1Al-0.2Ta-0.1V-0.1Mn-0.1C.
[0032] According to the mass ratio, the alloy constituent elements other than Y and Ti are used as raw materials, put into the induction furnace of the atomization equipment, and evacuated to a vacuum degree of 8.9×10 -2 Pa, then filled with ultra-high purity H with a purity of 99.9999% 2 to 0.03MPa, heat and turn on the electromagnetic stirring until the alloy raw materials are completely melted, then add Y and Ti to the melt, and then evacuate to 9.9×10 -2 Pa, followed by atomization and pulverization. The atomization gas is argon, the atomization pressure is 6.5MPa, the flow rate of the alloy liquid is 0.32kg / s, and the average particle size of the atomized alloy powder is ~103μm. The atomized alloy powder is detected by X-diffraction, which shows that the alloy elements including Y and Ti are all solid s...
Embodiment 3
[0034] A nanostructured oxide dispersion strengthened martensite / ferrite dual phase steel was prepared, and the alloy composition was Fe-12Cr-2W-0.3Ti-0.8Y-4Al-0.3V-0.1Ta-0.4Mn-0.1N.
[0035] According to the mass ratio, the alloy constituent elements other than Y and Ti are used as raw materials, put into the induction furnace of the atomization equipment, and evacuated to a vacuum degree of 9.7×10 -2 Pa, then filled with ultra-high purity H with a purity of 99.9999% 2 to 0.03MPa, heat and turn on the electromagnetic stirring until the alloy raw materials are completely melted, then add Y and Ti to the melt, and then vacuum again to 9.7×10 -2 Pa, followed by atomization and pulverization. The atomization uses argon gas, the atomization pressure is 6.0MPa, the flow rate of the alloy liquid is 0.33kg / s, and the average particle size of the atomized alloy powder is ~110μm. The atomized alloy powder is detected by X-diffraction, which shows that all alloy elements including Y a...
PUM
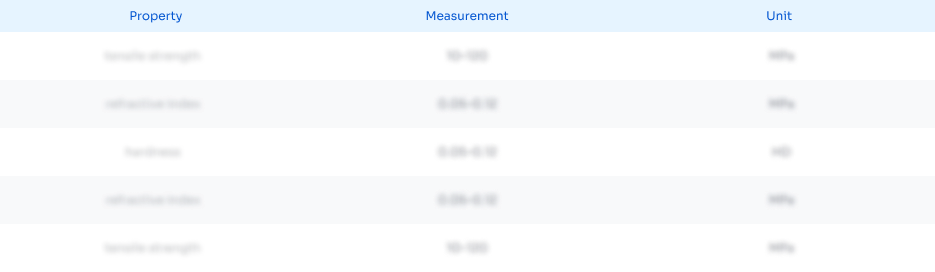
Abstract
Description
Claims
Application Information

- Generate Ideas
- Intellectual Property
- Life Sciences
- Materials
- Tech Scout
- Unparalleled Data Quality
- Higher Quality Content
- 60% Fewer Hallucinations
Browse by: Latest US Patents, China's latest patents, Technical Efficacy Thesaurus, Application Domain, Technology Topic, Popular Technical Reports.
© 2025 PatSnap. All rights reserved.Legal|Privacy policy|Modern Slavery Act Transparency Statement|Sitemap|About US| Contact US: help@patsnap.com