Manufacture method of selective emitter crystalline silicon solar cells
A technology of solar cells and emitters, applied in the field of solar cells, can solve the problems of high temperature damage of silicon wafers, high cost, complicated process, etc., and achieve the effects of saving equipment cost, low cost and few process steps.
- Summary
- Abstract
- Description
- Claims
- Application Information
AI Technical Summary
Problems solved by technology
Method used
Image
Examples
Embodiment 1
[0032]The surface of the silicon wafer is cleaned and textured, and a p-n junction with a diffusion square resistance of 110ohm / sq is produced by controlling the diffusion temperature, gas flow rate and process time of the diffusion furnace. The p-n junction with a diffusion resistance of 110ohm / sq is subjected to steps such as plasma edge etching, surface removal of silicon-phosphorus glass, preparation of an anti-reflection layer, and then printing the positive electrode, the back electrode, and the back electric field. When printing the back electrode, use silver paste with a silver solid content of 70% and a phosphorus content of 2% for printing, and then sinter at 750°C, so that the P atoms on the silicon wafer where the positive electrode is printed are further diffused, and the diffusion resistance It is 55ohm / sq, and the diffusion resistance is 110ohm / sq on the part where the positive electrode is not printed, so that a deep and shallow p-n junction is obtained.
PUM
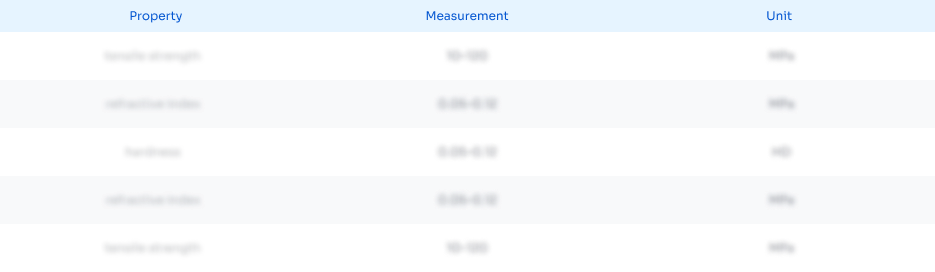
Abstract
Description
Claims
Application Information

- R&D
- Intellectual Property
- Life Sciences
- Materials
- Tech Scout
- Unparalleled Data Quality
- Higher Quality Content
- 60% Fewer Hallucinations
Browse by: Latest US Patents, China's latest patents, Technical Efficacy Thesaurus, Application Domain, Technology Topic, Popular Technical Reports.
© 2025 PatSnap. All rights reserved.Legal|Privacy policy|Modern Slavery Act Transparency Statement|Sitemap|About US| Contact US: help@patsnap.com