Preparation method of MMA-BMA-MAA (methyl methacrylate-n-butyl methacrylate-methacrylic acid) ternary copolymer resin
A ternary copolymer resin and molecular weight regulator technology, applied in the direction of coating, can solve the problems of loss, consumption, loss of effectiveness of dispersant, etc., to achieve uniform heat dissipation, improved adhesion, and smooth and controllable reaction.
- Summary
- Abstract
- Description
- Claims
- Application Information
AI Technical Summary
Problems solved by technology
Method used
Examples
Embodiment 1
[0018] (1) Ingredients: 80 parts of MMA, 20 parts of BMA, 0.8 parts of MAA, 1.2 parts of initiator, 0.8 parts of molecular weight regulator, 1 part of auxiliary dispersant, 8 parts of dispersant and 180 parts of deionized water are used for later use.
[0019] Wherein, the dispersant is polyvinyl alcohol, the auxiliary dispersant is one or more of C6-C14 higher alcohols, the molecular weight regulator is n-dodecanethiol, and the initiator is azobisisobutyronitrile.
[0020] (2) Reaction: Put all the deionized water and dispersant prepared in step (1) into the kettle, start stirring, and raise the temperature to 40°C. All MMA, BMA, MAA, molecular weight regulator and initiator are added into the reactor, and the temperature inside the reactor is kept at 40° C., and stirred for 50 minutes. Afterwards, the temperature was raised to 70°C, and the dispersant was put into the kettle after reacting at this temperature for 45 minutes. After the reaction was continued for 4 hours, the ...
Embodiment 2
[0024] (1) Ingredients: 95 parts of MMA, 5.5 parts of BMA, 1.5 parts of MAA, 1.8 parts of initiator, 2 parts of molecular weight modifier, 2 parts of co-dispersing agent, 7 parts of dispersing agent and 180 parts of deionized water, set aside.
[0025] Wherein, the dispersant is ethyl cellulose, the auxiliary dispersant is one or more of C6-C14 higher alcohols, the molecular weight regulator is n-dodecanethiol, and the initiator is azobisisobutyronitrile.
[0026] (2) Reaction: Put all the deionized water and dispersant prepared in step (1) into the kettle, start stirring, and raise the temperature to 50°C. All MMA, BMA, MAA, molecular weight regulator and initiator are added into the reactor, and the temperature inside the reactor is kept at 50° C., and stirred for 45 minutes. Afterwards, the temperature was raised to 75°C, and after reacting at this temperature for 40 minutes, the dispersant was put into the kettle, and after the reaction was continued for 4 hours, the tempe...
Embodiment 3
[0030] (1) Ingredients: 75 parts of MMA, 25 parts of BMA, 0.5 part of MAA, 2 parts of molecular weight modifier, 0.3 part of initiator, 10 parts of dispersant, 0.5 part of auxiliary dispersant and 250 parts of deionized water, set aside;
[0031] The dispersant is a graft copolymer of polyvinylpyrrolidone and methylcellulose; the molecular weight regulator is n-dodecanethiol; the auxiliary dispersant is one or a mixture of higher alcohols of C6-C14; The initiator is azobisisobutyronitrile.
[0032] (2) Reaction: first add the deionized water and dispersing agent prepared in step (1) into the reaction kettle, start stirring, and raise the temperature to 45°C; put all the initiator, molecular weight regulator, MMA, BMA and MAA into the reactor Put into the reaction kettle, stir at 30-50°C for 30-60 minutes, then raise the temperature to 65°C, react for 70 minutes, add the dispersant to the kettle, and continue the reaction for 4 hours. Then the temperature was raised to 78°C fo...
PUM
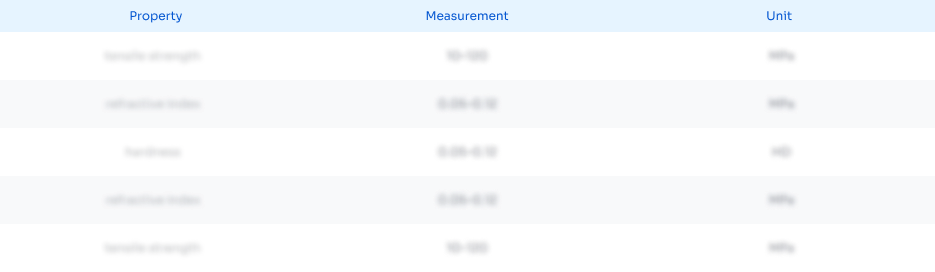
Abstract
Description
Claims
Application Information

- R&D Engineer
- R&D Manager
- IP Professional
- Industry Leading Data Capabilities
- Powerful AI technology
- Patent DNA Extraction
Browse by: Latest US Patents, China's latest patents, Technical Efficacy Thesaurus, Application Domain, Technology Topic, Popular Technical Reports.
© 2024 PatSnap. All rights reserved.Legal|Privacy policy|Modern Slavery Act Transparency Statement|Sitemap|About US| Contact US: help@patsnap.com