Luminous display back plane, method for preparing pixel definition layer thereof and display device
A pixel-defining layer and light-emitting display technology, applied in lighting devices, optomechanical equipment, electroluminescent light sources, etc., can solve the problems of increasing the number of masks used, increasing the exposure process, and unfavorable mass production
- Summary
- Abstract
- Description
- Claims
- Application Information
AI Technical Summary
Problems solved by technology
Method used
Image
Examples
Embodiment 1
[0045] An embodiment of the present invention provides a light-emitting display backplane, such as figure 1 and figure 2 As shown, the backplane includes: a substrate 10 and a pixel defining layer 11 disposed on the substrate 10, and the pixel defining layer 11 includes:
[0046] A photosensitive resin layer 111 and a transparent boundary layer 112 arranged sequentially from bottom to top;
[0047] The photosensitive resin layer 111 and the transparent delimiting layer 112 are provided with openings in corresponding regions of each pixel, and the openings of the transparent delimiting layer 112 are smaller than the openings of the photosensitive resin layer 111, so as to form a luminescent material filling domain 12 that is wide at the bottom and narrow at the top. .
[0048] The light-emitting display backplane includes a substrate, an ITO (Indium Tin Oxide, indium tin oxide) anode, a light-emitting layer, a cathode, and the like. Among them, when forming the light-emitti...
Embodiment 2
[0058] An embodiment of the present invention provides a method for preparing a pixel defining layer of a light-emitting display backplane. The light-emitting display backplane includes: a substrate and a pixel defining layer disposed on the substrate, such as image 3 As shown, the method includes:
[0059] Step 201, sequentially forming the photosensitive resin layer 111 and the transparent boundary layer 112, such as Figure 4 shown;
[0060] This step forms the lowermost photosensitive resin 111 and the transparent defining layer 112 on it, and the way to form (or prepare) these film layers can be physical vapor deposition (PVD) methods such as evaporation, sputtering, ion plating, etc. It may also be a chemical vapor deposition (CVD) method, generally selected according to the material of the film to be deposited, which is not limited in this embodiment. Taking the transparent defining layer 112 as an example of a silicon nitride film, a specific preparation scheme is a...
PUM
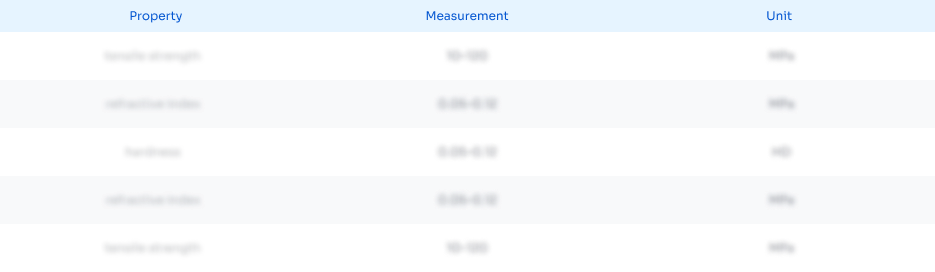
Abstract
Description
Claims
Application Information

- R&D
- Intellectual Property
- Life Sciences
- Materials
- Tech Scout
- Unparalleled Data Quality
- Higher Quality Content
- 60% Fewer Hallucinations
Browse by: Latest US Patents, China's latest patents, Technical Efficacy Thesaurus, Application Domain, Technology Topic, Popular Technical Reports.
© 2025 PatSnap. All rights reserved.Legal|Privacy policy|Modern Slavery Act Transparency Statement|Sitemap|About US| Contact US: help@patsnap.com