Method for reinforcing nickel-base alloy layer on aluminum alloy surface
A technology of aluminum alloy surface and nickel-based alloy, applied in the direction of metal material coating process, coating, etc., can solve the problems of low bonding strength, cracking, falling off, etc., and achieve the effect of expanding the scope of application
- Summary
- Abstract
- Description
- Claims
- Application Information
AI Technical Summary
Problems solved by technology
Method used
Examples
Embodiment approach
[0020] The second embodiment of the present invention: the surface treatment of the aluminum alloy substrate is carried out first, and the treatment process still adopts a mechanical and chemical mixed method to eliminate the oxide film on the surface of the aluminum alloy. Sand grinding→ultrasonic cleaning→chemical reagent cleaning→drying. The chemical reagent cleaning is to soak the aluminum alloy substrate in NaOH solution at 65°C for 5 minutes and then take it out and dry it.
[0021] Prepare an aluminum alloy nickel-based alloy layer cladding material containing rare earths La and Ce. The formula of the nickel-based alloy cladding material is measured by weight percentage, and its composition is: 2.5% of rare earth La and Ce, and 0.7% to 0.8% of C , Si3.0%~3.5%, W3.5%~6.5%, Cr12%~16%, Fe<15%, the rest is Ni, impurity<1%. Mix the above powders, put them into a ball mill and mill them for 15 hours, take them out and add an alcohol binder, stir them evenly to form a paste, t...
PUM
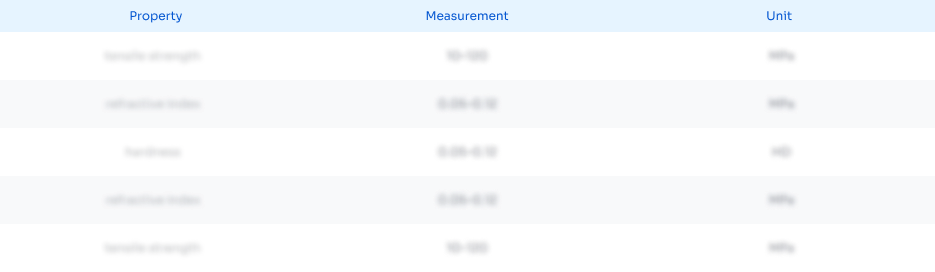
Abstract
Description
Claims
Application Information

- R&D
- Intellectual Property
- Life Sciences
- Materials
- Tech Scout
- Unparalleled Data Quality
- Higher Quality Content
- 60% Fewer Hallucinations
Browse by: Latest US Patents, China's latest patents, Technical Efficacy Thesaurus, Application Domain, Technology Topic, Popular Technical Reports.
© 2025 PatSnap. All rights reserved.Legal|Privacy policy|Modern Slavery Act Transparency Statement|Sitemap|About US| Contact US: help@patsnap.com