Process for recovering copper and zinc and tin and lead by utilizing side blown converter at the bottom
A side-blown furnace and process technology, applied in zinc, tin, lead processes, and copper in tin ore fields, can solve the problems of many operations, high remelting and high smelting costs, and achieve the effect of strong adaptability
- Summary
- Abstract
- Description
- Claims
- Application Information
AI Technical Summary
Problems solved by technology
Method used
Image
Examples
Embodiment 1
[0021] (1) Batching and mixing: analyze the chemical composition of slag, soot and low-grade tin respectively; mix the slag, soot, low-grade tin ore and flux evenly, and the moisture content of the material is ≤3%;
[0022] (2) Reduction smelting volatilized lead, zinc, lead and zinc fume collection: first add the hot slag of the reduction furnace to the side blowing furnace, then add the mixed materials into the side blowing furnace and the hot slag of the reduction furnace to mix, and then reduce and smelt. Add the hot slag of the reduction furnace in the side-blown furnace and the tin content of the material after the batching and mixing is 10%, and the silicic acidity of the slag is 1-1.2; the first stage reduces and smelts volatile lead and zinc, and collects dust to obtain lead oxide and zinc oxide. Lead and zinc fumes are collected through cloth bags, and the dust content of the flue gas after dust collection is ≤50mg / Nm 3 ;Reductant bituminous coal particle size in red...
PUM
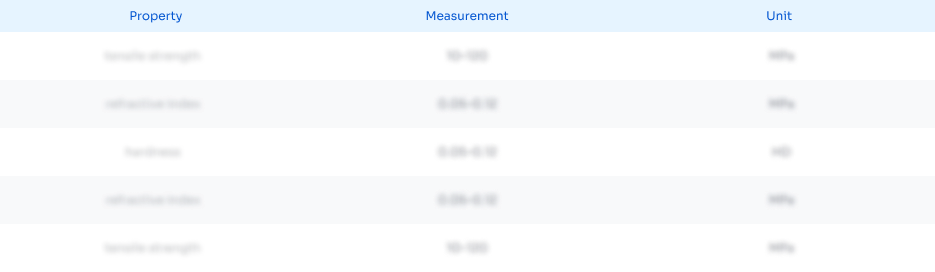
Abstract
Description
Claims
Application Information

- R&D
- Intellectual Property
- Life Sciences
- Materials
- Tech Scout
- Unparalleled Data Quality
- Higher Quality Content
- 60% Fewer Hallucinations
Browse by: Latest US Patents, China's latest patents, Technical Efficacy Thesaurus, Application Domain, Technology Topic, Popular Technical Reports.
© 2025 PatSnap. All rights reserved.Legal|Privacy policy|Modern Slavery Act Transparency Statement|Sitemap|About US| Contact US: help@patsnap.com