Zinc-boron-silicon system heat-resisting environmental-friendly emulsion opal glass and preparation method thereof
An opaque glass, zinc borosilicate technology, applied in glass manufacturing equipment, glass production, glass molding and other directions, can solve problems such as unfavorable industrial large-scale continuous production, large energy consumption, instability and other problems, and achieve continuous industrialization. The effect of production, saving energy and resources, and improving production efficiency
- Summary
- Abstract
- Description
- Claims
- Application Information
AI Technical Summary
Problems solved by technology
Method used
Image
Examples
Embodiment 1
[0025] Oxide
[0026] The glass batch prepared according to the above components was melted at 1550°C for 3 hours, poured and formed into original glass, and annealed for 1 hour to obtain heat-resistant and environmentally friendly opaque glass.
Embodiment 2
[0028] Oxide
[0029] The glass batch prepared according to the above components was melted at 1450°C for 4 hours, poured into original glass, and annealed for 1 hour to obtain heat-resistant and environmentally friendly opaque glass.
PUM
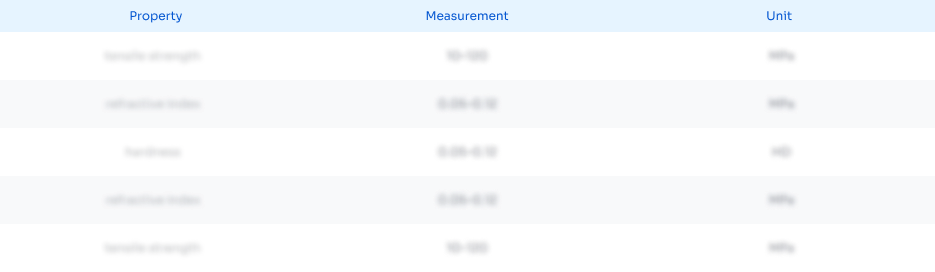
Abstract
Description
Claims
Application Information

- R&D
- Intellectual Property
- Life Sciences
- Materials
- Tech Scout
- Unparalleled Data Quality
- Higher Quality Content
- 60% Fewer Hallucinations
Browse by: Latest US Patents, China's latest patents, Technical Efficacy Thesaurus, Application Domain, Technology Topic, Popular Technical Reports.
© 2025 PatSnap. All rights reserved.Legal|Privacy policy|Modern Slavery Act Transparency Statement|Sitemap|About US| Contact US: help@patsnap.com