Compounded denitration catalyst, as well as preparation method and application thereof
A denitration catalyst and composite technology, applied in chemical instruments and methods, physical/chemical process catalysts, separation methods, etc., can solve the problems of low denitrification performance of catalysts, high toxicity of precursors, and high cost of catalysts, and improve low-temperature denitrification performance , Improve the safety of use and reduce the cost
- Summary
- Abstract
- Description
- Claims
- Application Information
AI Technical Summary
Problems solved by technology
Method used
Image
Examples
Embodiment 1
[0017] Example 1: 10wt%CeO 2 -5wt%MoO 3 / TiO 2 Preparation of composite catalyst
[0018] a) Take 4.96ml of 0.03 mol / L ammonium molybdate solution and stir in a 30°C water bath; then add 2.55g of titanium dioxide into the solution and stir for 4 hours to obtain a slurry.
[0019] b) drying the slurry prepared in step a) at 120° C. for 12 hours to prepare a dry sample. The sample was baked in a muffle furnace at 500°C for 4 hours, and after cooling, the sample was ground into powder.
[0020] c) Take 2.18ml of 0.80 mol / L cerium nitrate solution, stir in a 30°C water bath; then add the powder obtained in b) into the solution, and stir for 4 hours to obtain a slurry.
[0021] d) Dry the slurry prepared in step c) at 120°C for 12 hours, and then bake it in a muffle furnace at 500°C for 4 hours to obtain CeO 2 -MoO 3 / TiO 2 catalyst.
Embodiment 2
[0022] Example 2: 10wt%CeO 2 -2wt%MoO 3 / TiO 2 Preparation of composite catalyst
[0023] a) Take 2.98 ml of 0.02 mol / L ammonium molybdate solution, stir in a 30°C water bath; then add 2.55 g of titanium dioxide into the solution, and stir for 4 hours to obtain a slurry.
[0024] b) drying the slurry prepared in step a) at 120° C. for 12 hours to prepare a dry sample. The sample was baked in a muffle furnace at 500°C for 4 hours, and after cooling, the sample was ground into powder.
[0025] c) Take 2.18 ml of 0.80 mol / L cerium nitrate solution, stir in a 30°C water bath; then add the powder obtained in b) into the solution, and stir for 4 hours to obtain a slurry.
[0026] d) Dry the slurry prepared in step c) at 120°C for 24 hours, and then bake it in a muffle furnace at 500°C for 4 hours to obtain CeO 2 -MoO 3 / TiO 2 catalyst.
Embodiment 3
[0027] Example 3: 10wt%CeO 2 -8wt%MoO 3 / TiO 2 Preparation of composite catalyst
[0028] a) Take 1.86 ml of 0.05 mol / L ammonium molybdate solution, stir in a 30°C water bath; then add 2.55 g of titanium dioxide into the solution, and stir for 4 hours to obtain a slurry.
[0029] b) drying the slurry prepared in step a) at 120° C. for 18 hours to prepare a dry sample. The sample was baked in a muffle furnace at 500°C for 4 hours, and after cooling, the sample was ground into powder.
[0030] c) Take 2.18 ml of 0.80 mol / L cerium nitrate solution, stir in a 30°C water bath; then add the powder obtained in b) into the solution, and stir for 4 hours to obtain a slurry.
[0031] d) Dry the slurry prepared in step c) at 120°C for 24 hours, and then bake it in a muffle furnace at 500°C for 4 hours to obtain CeO 2 -MoO 3 / TiO 2 catalyst.
PUM
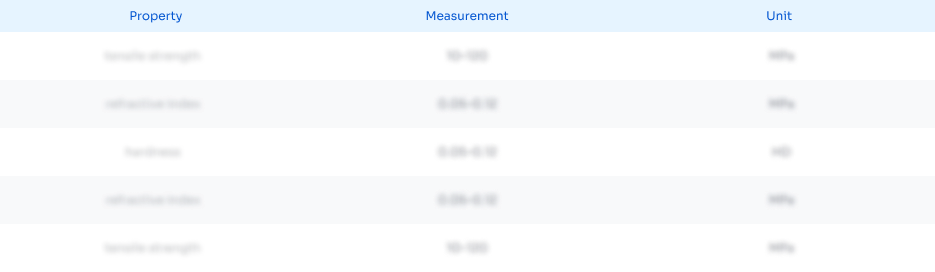
Abstract
Description
Claims
Application Information

- R&D
- Intellectual Property
- Life Sciences
- Materials
- Tech Scout
- Unparalleled Data Quality
- Higher Quality Content
- 60% Fewer Hallucinations
Browse by: Latest US Patents, China's latest patents, Technical Efficacy Thesaurus, Application Domain, Technology Topic, Popular Technical Reports.
© 2025 PatSnap. All rights reserved.Legal|Privacy policy|Modern Slavery Act Transparency Statement|Sitemap|About US| Contact US: help@patsnap.com