Preparation method of full-solid-state nano composite polymer electrolyte
A nanocomposite and polymer technology, applied in the direction of nanotechnology, nanotechnology, nanotechnology for materials and surface science, etc., can solve the problems of limiting the electrical properties of composite polymer electrolytes, uneven dispersion, and easy agglomeration, etc. Achieve good cycle stability, smooth surface, high room temperature conductivity and ion mobility
- Summary
- Abstract
- Description
- Claims
- Application Information
AI Technical Summary
Problems solved by technology
Method used
Examples
Embodiment 1
[0026] After the graphene oxide is functionalized, it is uniformly mixed with the matrix, lithium salt, and solvent at room temperature to obtain a composite sol, and the solvent is automatically volatilized and dried under the protection of nitrogen to obtain a solid polymer electrolyte membrane.
[0027] Step (1): Weigh 100mg of graphene oxide and disperse it in 200ml of tetrahydrofuran, and process it under 30kHz ultrasonic wave for 10 minutes to obtain a graphene oxide dispersion, add 2g of polyethylene glycol monomethyl ether, and process it under 30kHz ultrasonic wave for 10 minutes , add 50 mg of catalyst dicyclohexylcarbodiimide, stir mechanically at room temperature for 2 hours, raise the temperature to 60°C, stir and reflux for 24 hours, dilute and wash with deionization, filter with ultra-microporous membrane, and repeat with ethanol Washing and suction filtration, vacuum drying at 50°C for 48 hours to obtain functionalized graphene;
[0028] Step (2): Weigh 5mg...
Embodiment 2
[0031] After the graphene oxide is functionalized, it is uniformly mixed with the matrix, lithium salt, and solvent at room temperature to obtain a composite sol, and the solvent is naturally volatilized and dried under the protection of nitrogen to obtain a solid polymer electrolyte membrane.
[0032] Step (1): Weigh 100 mg of graphene oxide and disperse it in 200 ml of tetrahydrofuran, and process it under 40 kHz ultrasonic wave for 5 minutes to obtain a graphene oxide dispersion, add 1.5 g of polyethylene glycol monomethyl ether, and process it under 40 kHz ultrasonic wave for 5 minutes. Minutes, add 50 mg of dicyclohexylcarbodiimide as a catalyst, mechanically stir for 4 hours at room temperature, raise the temperature to 60°C, stir and reflux for 24 hours, dilute and wash with deionization, filter with ultra-microporous membrane, and then use Repeated washing and suction filtration with ethanol, vacuum drying at 50°C for 48 hours to obtain functionalized graphene;
...
Embodiment 3
[0036] After the graphene oxide is functionalized, it is uniformly mixed with the matrix, lithium salt, and solvent at room temperature to obtain a composite sol, and the solvent is automatically volatilized and dried under nitrogen protection to obtain a solid polymer electrolyte membrane.
[0037]Step (1): Weigh 100 mg of graphene oxide and disperse it in 200 ml of tetrahydrofuran, and process it under 40 kHz ultrasonic wave for 5 minutes to obtain a graphene oxide dispersion, add 1.5 g of polyethylene glycol monomethyl ether, and process it under 40 kHz ultrasonic wave for 5 minutes. Minutes, add 50 mg of dicyclohexylcarbodiimide as a catalyst, mechanically stir for 4 hours at room temperature, raise the temperature to 60°C, stir and reflux for 24 hours, dilute and wash with deionization, filter with ultra-microporous membrane, and then use Repeated washing and suction filtration with ethanol, vacuum drying at 50°C for 48 hours to obtain functionalized graphene;
[00...
PUM
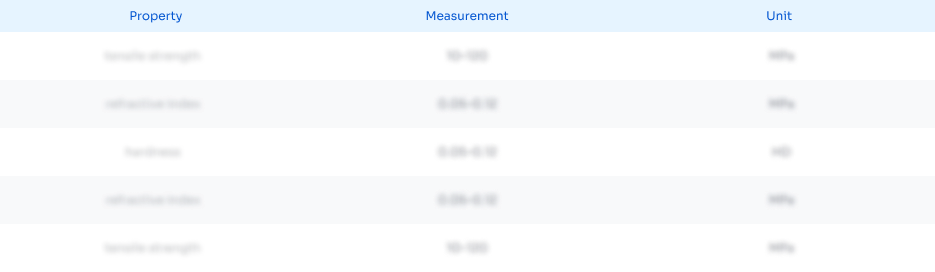
Abstract
Description
Claims
Application Information

- Generate Ideas
- Intellectual Property
- Life Sciences
- Materials
- Tech Scout
- Unparalleled Data Quality
- Higher Quality Content
- 60% Fewer Hallucinations
Browse by: Latest US Patents, China's latest patents, Technical Efficacy Thesaurus, Application Domain, Technology Topic, Popular Technical Reports.
© 2025 PatSnap. All rights reserved.Legal|Privacy policy|Modern Slavery Act Transparency Statement|Sitemap|About US| Contact US: help@patsnap.com