Preparation method of lightweight composite wallboard
A composite wallboard and composite wall technology, applied in the direction of chemical instruments and methods, manufacturing tools, synthetic resin layered products, etc., can solve the difficulty in adjusting the size of the formed wallboard, the discontinuous production process of the wallboard, and the hollowing and falling off, etc. problems, to achieve the effect of ideal overall mechanical strength, ideal anti-seismic function, and improved flexural strength
- Summary
- Abstract
- Description
- Claims
- Application Information
AI Technical Summary
Problems solved by technology
Method used
Image
Examples
Embodiment Construction
[0039] The present invention proposes a production method of lightweight composite wallboard. The forming process is to assemble a flat support plate 1 and a combined baffle plate 2 for rolling forming of a flat die into a set, which can form a shape with tenons and notches on both sides. Wallboard blank body forming mold 3, and then the forming mold 3 is put on the assembly line conveying platform 4, and the bottom light aggregate concrete feeding system 5, the bottom light aggregate concrete feeding system 5, and the bottom light aggregate concrete are successively arranged on the top of the assembly line conveying platform 4 along the direction of the assembly line. Rolling system 6, reinforced mesh laying system 7, upper light aggregate concrete feeding system 8, upper light aggregate concrete rolling system 9, surface mortar feeding system 10, glass mesh cloth laying system 11, The surface layer mortar rolling system 12 and the plastic film laying system 13, when the formi...
PUM
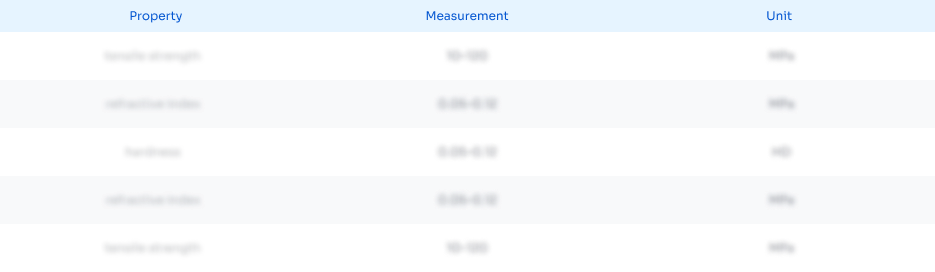
Abstract
Description
Claims
Application Information

- Generate Ideas
- Intellectual Property
- Life Sciences
- Materials
- Tech Scout
- Unparalleled Data Quality
- Higher Quality Content
- 60% Fewer Hallucinations
Browse by: Latest US Patents, China's latest patents, Technical Efficacy Thesaurus, Application Domain, Technology Topic, Popular Technical Reports.
© 2025 PatSnap. All rights reserved.Legal|Privacy policy|Modern Slavery Act Transparency Statement|Sitemap|About US| Contact US: help@patsnap.com