Secondary cooling method for reducing transverse cracks of corners of microalloy sheet billet
A secondary cooling and micro-alloy steel technology, applied in the field of continuous casting secondary cooling, can solve the problems of high cooling intensity, low billet temperature, and reduced plasticity, achieve high cooling speed, uniform precipitates, and improve high-temperature mechanical properties Effect
- Summary
- Abstract
- Description
- Claims
- Application Information
AI Technical Summary
Problems solved by technology
Method used
Examples
example 1
[0029] The casting steel type is boron-containing steel 45B, the cross-sectional size is 1600mm×200mm, and the casting speed is 1.1m / min. The secondary cooling method of the present invention is adopted: after the billet exits the mold, the temperature of the mold exit is 1000°C. Adjust the water volume of the wide side to 362L / min, the water volume of the narrow side to 72L / min, and the cooling time to 80s, so that the casting slab is cooled rapidly at a cooling rate of 4°C / s in the vertical section of the casting machine, and the cooling temperature of the casting slab reaches 680°C ;Subsequently reduce the amount of cooling water for the slab, use a water meter with a specific water volume of 0.7L / kg to pour, use the latent heat of solidification of the slab to warm the slab at a speed of 2°C / s, and reach 880°C when the slab exits the vertical section Above, the final slab enters the subsequent secondary cooling zone in the slow cooling mode (the specific water volume is 0.8...
example 2
[0032]The cast steel type is vanadium-containing steel 15MnV, the cross-sectional size is 1800mm×220mm, and the casting speed is 0.9m / min. The secondary cooling method of the present invention is adopted: after the billet exits the mold, the temperature of the mold exit is 1050°C. Adjust the water volume of the wide side to 380L / min, the water volume of the narrow side to 80L / min, and the cooling time to 74s, so that the casting slab is cooled rapidly at a cooling rate of 5°C / s in the vertical section of the casting machine, and the cooling temperature of the casting slab reaches 680°C . Then the slab reduces the amount of cooling water for the slab, pours with a water meter with a specific water volume of 0.7L / kg, and uses the latent heat of solidification of the slab to return the temperature of the slab. The temperature recovery speed is 3°C / s. When the slab exits the vertical section, it reaches above 900°C , the final slab enters the subsequent secondary cooling zone in s...
PUM
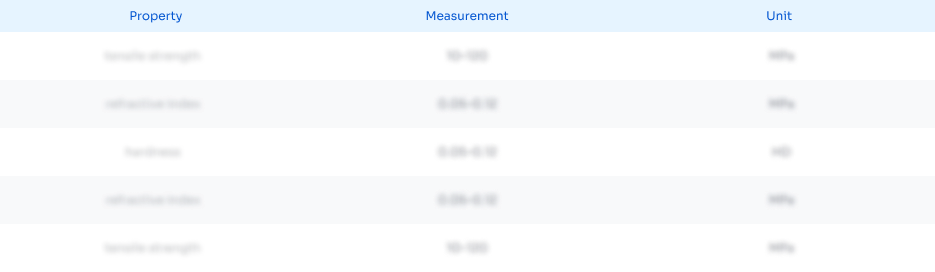
Abstract
Description
Claims
Application Information

- Generate Ideas
- Intellectual Property
- Life Sciences
- Materials
- Tech Scout
- Unparalleled Data Quality
- Higher Quality Content
- 60% Fewer Hallucinations
Browse by: Latest US Patents, China's latest patents, Technical Efficacy Thesaurus, Application Domain, Technology Topic, Popular Technical Reports.
© 2025 PatSnap. All rights reserved.Legal|Privacy policy|Modern Slavery Act Transparency Statement|Sitemap|About US| Contact US: help@patsnap.com