Method for refining waste paperboard pyrolytic oil
A refining method and pyrolysis oil technology, which is applied in the petroleum industry, hydrocarbon oil treatment, hydrotreating process, etc., can solve the problems affecting the next start of the engine, affecting the atomization effect of the emulsion, and affecting the stability of the emulsion. Achieve the effect of low equipment requirements, stable properties, reduced acidity and corrosion
- Summary
- Abstract
- Description
- Claims
- Application Information
AI Technical Summary
Problems solved by technology
Method used
Image
Examples
Embodiment 1
[0023] Slowly add 30ml of ether solution into 10ml of waste cardboard pyrolysis crude oil, after mixing for a period of time, let the mixture stand for 20min, and the pyrolysis crude oil component is divided into upper and lower layers. Take the upper layer mixture and carry out rotary evaporation to recover the solvent ether, and obtain the ether soluble fraction.
[0024] SiO with a mass ratio of 4:6 2 / TiO 2 Dissolved in ethanol and mixed for 1h, dried to obtain SiO 2 / TiO 2 catalyst. La with a molar ratio of 5% 2 o 3 Soluble in 0.8mol / L H 2 SO 4 solution, according to 10mL La 3+ -H 2 SO 4 Impregnate at a ratio of 5g catalyst, mix for 1h, bake at 450°C for 6h after drying, and obtain solid superacid SO after cooling 4 2- / TiO 2 -SiO 2 -La 3+ .
[0025] Add 20 g of ether solubles, 5 g of ethanol (analytically pure) and 1 g of solid acid catalyst into a three-neck round bottom flask, and react for 3 hours at a temperature of 70 ° C. After the reaction, the mi...
Embodiment 2
[0028] Slowly add 30ml of ether solution into 10ml of waste cardboard pyrolysis crude oil, after mixing for a period of time, let the mixture stand for 20min, and the pyrolysis crude oil component is divided into upper and lower layers. Take the upper layer mixture and carry out rotary evaporation to recover the solvent ether, and obtain the ether soluble fraction.
[0029] SiO with a mass ratio of 4:6 2 / TiO 2 Dissolved in ethanol and mixed for 1h, dried to obtain SiO 2 / TiO 2 catalyst. La with a molar ratio of 7% 2 o 3 Soluble in 0.8mol / L H 2 SO 4 solution, according to 10mL La 3+ -H 2 SO 4 Impregnate at a ratio of 5g catalyst, mix for 1h, bake at 450°C for 6h after drying, and obtain solid superacid SO after cooling 4 2- / TiO 2 -SiO 2 -La 3+ .
[0030] Add 20 g of ether solubles, 5 g of ethanol (analytically pure) and 1 g of solid acid catalyst into a three-neck round bottom flask, and react for 3 hours at a temperature of 70 ° C. After the reaction, the mi...
Embodiment 3
[0033] Slowly add 30ml of ether solution into 10ml of waste cardboard pyrolysis crude oil, after mixing for a period of time, let the mixture stand for 20min, and the pyrolysis crude oil component is divided into upper and lower layers. Take the upper layer mixture and carry out rotary evaporation to recover the solvent ether, and obtain the ether soluble fraction.
[0034] SiO with a mass ratio of 4:6 2 / TiO 2 Dissolved in ethanol and mixed for 1h, dried to obtain SiO 2 / TiO 2 catalyst. La with a molar ratio of 5% 2 o 3 Soluble in 0.8mol / L H 2 SO 4solution, according to 10mL La 3+ -H 2 SO 4 Impregnate at a ratio of 5g catalyst, mix for 1h, bake at 450°C for 6h after drying, and obtain solid superacid SO after cooling 4 2- / TiO 2 -SiO 2 -La 3+ .
[0035] Add 20 g of ether solubles, 5 g of ethanol (analytically pure) and 1 g of solid acid catalyst into a three-neck round bottom flask, and react for 3 hours at a temperature of 70 ° C. After the reaction, the mix...
PUM
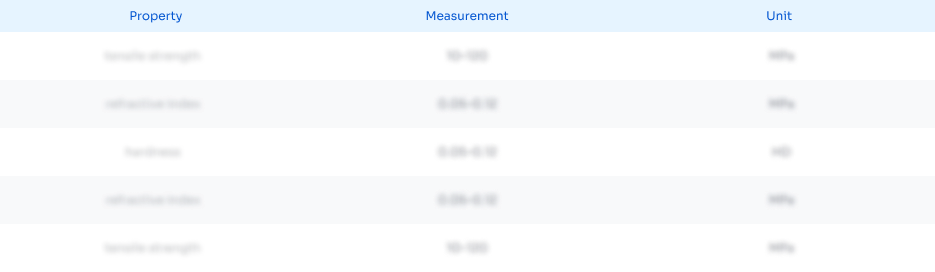
Abstract
Description
Claims
Application Information

- R&D Engineer
- R&D Manager
- IP Professional
- Industry Leading Data Capabilities
- Powerful AI technology
- Patent DNA Extraction
Browse by: Latest US Patents, China's latest patents, Technical Efficacy Thesaurus, Application Domain, Technology Topic, Popular Technical Reports.
© 2024 PatSnap. All rights reserved.Legal|Privacy policy|Modern Slavery Act Transparency Statement|Sitemap|About US| Contact US: help@patsnap.com