Microwave dielectric ceramic powder and preparation method thereof
A technology of microwave dielectric ceramics and powders, applied in ceramics, inorganic insulators, etc., can solve the problems of restricting product production conditions and high sintering temperature, and achieve the effects of simple composition and preparation, improved quality coefficient, and good dielectric properties
- Summary
- Abstract
- Description
- Claims
- Application Information
AI Technical Summary
Problems solved by technology
Method used
Examples
preparation example Construction
[0017] The invention provides a microwave dielectric ceramic powder and a preparation method thereof, specifically ZnO-MgO-TiO doped with 85-96% by weight of strontium and cobalt 2 The ternary system microwave dielectric material is composed of 4-15% by weight zinc barium borosilicate flux.
[0018] Preferably, ZnO, MgO and TiO 2 The molar percentage ratio is 1:2:3.
[0019] Preferably, the strontium and cobalt are doped in a molar percentage of 1.5-6% SrO and 0-7% CoO.
[0020] Preferably, the zinc barium borosilicate flux is composed of 10-50% Li by mole percent 2 O, 10-40% ZnO, 10-30% BaO, 15-40% B 2 o 3 , 10-35% SiO 2 composition.
[0021] Preferably, the composition form of the flux element is an oxide, a carbonate compound and / or a compound.
[0022] At the same time, a method for preparing microwave dielectric ceramic powder is provided, including:
[0023] According to the stoichiometric ratio of the main ceramic powder ZnO: (MgCO 3 ) 4 ·Mg(OH) 2 5H2O:TiO 2...
Embodiment 1
[0028] (1) According to the stoichiometric ratio of the main ceramic powder ZnO: (MgCO 3 ) 4 ·Mg(OH) 2 5H2O:TiO 2 =15:7:50, then doped with 1.5%SrCO 3 , 7% CoCO 3 With the main porcelain powder in alcohol as the medium, after ball milling for 24 hours, it was calcined gently at 800°C for 8 hours;
[0029] (2) According to the stoichiometric ratio of lithium zinc barium borosilicate flux, 50 mol% Li 2 O, 10 mol% ZnO, 10 mol% BaO, 15 mol% B 2 o 3 , 15 mol% SiO 2 . Mix the proportioned oxides and put them into a high-temperature furnace for calcination at 800°C, then cool the molten glass and pulverize it. With de-alcohol as the medium, after ball milling for 6 hours, dry at 120;
[0030] (3) The main powder synthesized in the second ball milling step (2), add 96% by weight of the main powder and 4% by weight of flux according to the stoichiometric ratio, add alcohol according to the weight ratio of powder to alcohol 1:2, and mix Ball milling for 6 hours;
[0031] (4)...
Embodiment 2
[0034] (1) According to the stoichiometric ratio of the main ceramic powder ZnO: (MgCO 3 ) 4 ·Mg(OH) 2 5H2O:TiO 2 =15:7:50, then doped with 2%SrCO 3 , 5% CoCO 3 Mix with the main porcelain powder, use deionized water as the medium, ball mill for 24 hours, then gently calcined at 800°C for 6 hours;
[0035] (2) According to the stoichiometric ratio of lithium zinc barium borosilicate flux, 20 mol% Li 2 O, 40 mol% ZnO, 10 mol% BaO, 10 mol% B 2 o 3 , 20 mol% SiO 2 ,. Mix the proportioned oxides and put them into a high-temperature furnace for calcination at 800°C, then water-quench the molten glass and pulverize it. Using deionized water as the medium, after ball milling for 7 hours, dry at 140°C;
[0036] (3) Secondary ball milling step (2) For the synthesized main powder, add 92% by weight of main powder and 8% by weight of flux according to the stoichiometric ratio, and add deionized powder according to the weight ratio of powder to deionized water 1:2 water, mixed an...
PUM
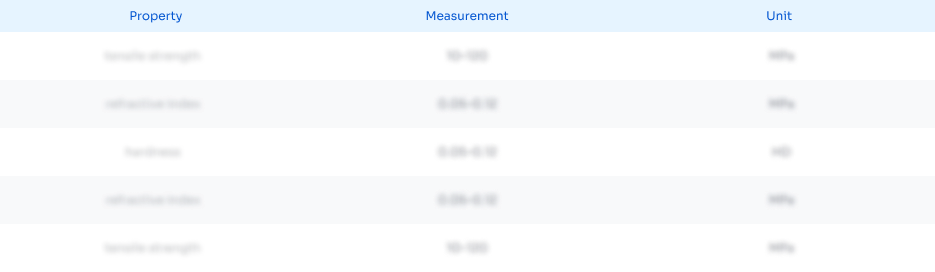
Abstract
Description
Claims
Application Information

- Generate Ideas
- Intellectual Property
- Life Sciences
- Materials
- Tech Scout
- Unparalleled Data Quality
- Higher Quality Content
- 60% Fewer Hallucinations
Browse by: Latest US Patents, China's latest patents, Technical Efficacy Thesaurus, Application Domain, Technology Topic, Popular Technical Reports.
© 2025 PatSnap. All rights reserved.Legal|Privacy policy|Modern Slavery Act Transparency Statement|Sitemap|About US| Contact US: help@patsnap.com