Smelting technique of brown corundum
A brown corundum and process technology, applied in the field of brown corundum smelting technology, can solve problems such as increasing the cost of raw materials, and achieve the effects of reducing smelting costs, reducing smelting power consumption and saving electricity bills
- Summary
- Abstract
- Description
- Claims
- Application Information
AI Technical Summary
Problems solved by technology
Method used
Examples
Embodiment 1
[0014] The smelting process of brown corundum of the present invention: it comprises the following steps:
[0015] The first step is to put the pulverized raw bauxite that meets the particle size requirements into a rotary kiln or a shaft kiln, and roast it to 1200°C with the heat provided by the gas generated by the generator;
[0016] In the second step, the calcined bauxite material is sent into the insulation material tank, and the carbon material and iron filings are added in proportion and then transferred into the insulation material bin;
[0017] The third step is to use the feeder to send the materials in the heat preservation bin in the second step into the electric furnace to continue heating and melting. After the reaction is complete, it is inspected, cooled and classified to obtain the finished product
Embodiment 2
[0019] The smelting process of brown corundum of the present invention, it comprises the following steps:
[0020] The first step is to mix the raw bauxite, carbon materials and iron scraps crushed to a fine particle size of 5mm in proportion, and roll them into balls with a diameter of 30-50mm, and then put them into a rotary kiln or a shaft kiln. The gas generated by the furnace provides heat to roast it to 1200°C;
[0021] In the second step, the roasted material is sent into the insulation material barrel and transferred into the insulation material bin;
[0022] The third step is to use the feeder to send the materials in the heat preservation silo in the second step into the electric furnace to continue heating and melting. After the reaction is complete, it is inspected, cooled and classified to obtain the finished product.
PUM
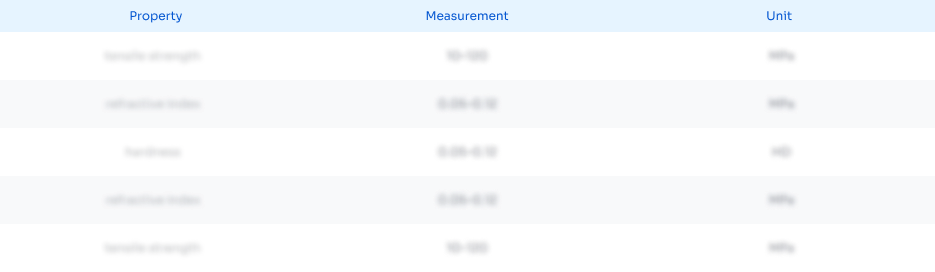
Abstract
Description
Claims
Application Information

- R&D
- Intellectual Property
- Life Sciences
- Materials
- Tech Scout
- Unparalleled Data Quality
- Higher Quality Content
- 60% Fewer Hallucinations
Browse by: Latest US Patents, China's latest patents, Technical Efficacy Thesaurus, Application Domain, Technology Topic, Popular Technical Reports.
© 2025 PatSnap. All rights reserved.Legal|Privacy policy|Modern Slavery Act Transparency Statement|Sitemap|About US| Contact US: help@patsnap.com