Preparation method of hot-rolled acid-washing high-strength steel for automobile carriage
A hot-rolled pickling, high-strength steel technology, applied in the fields of metal materials, steel smelting and controlled rolling and controlled cooling, can solve the problems of not being used for hot-rolled pickling, increasing production processes and costs, high Si content, etc. Good market development prospects, improved surface finish, good surface quality
- Summary
- Abstract
- Description
- Claims
- Application Information
AI Technical Summary
Problems solved by technology
Method used
Image
Examples
Embodiment 1
[0036] The specific composition of the cast slab in this embodiment is: C: 0.09%, Si: 0.03%, Mn: 1.79%, Mo: 0.16%, Nb: 0.048%, Ti: 0.16%, Al: 0.025%, B: 0.0025%, P: 0.006%, S: 0.006%, Ca: 0.004%, the rest is Fe and unavoidable impurities, of which the carbon equivalent Ceq=0.42, which ensures excellent weldability.
[0037] The specific production process is carried out according to the following steps:
[0038] 1) Billet heating: heat the billet to 1220~1260°C, keep it warm for 2h~2.5h, and austenitize the composition;
[0039] 2) Rolling in the recrystallization zone: the starting temperature of rolling in the recrystallization zone is 1150°C, rolling 3 passes, and the final rolling temperature in the recrystallization zone is controlled at 1030~1050°C to obtain an intermediate billet, which is then rolled in the recrystallization zone The reduction rate of each pass is controlled at 25%~40%.
[0040] 3) Rolling in the non-recrystallized area: when the intermediate billet ...
Embodiment 2
[0046] The specific composition of the cast slab in this embodiment is: C: 0.10%, Si: 0.02%, Mn: 1.70%, Mo: 0.15%, Nb: 0.050%, Ti: 0.18%, Al: 0.020%, B: 0.003%, P: 0.006%, S: 0.006%, Ca: 0.006%, the rest is Fe and unavoidable impurities, of which the carbon equivalent Ceq=0.41, which ensures excellent weldability.
[0047] The specific production process is carried out according to the following steps:
[0048] 1) Billet heating: heat the billet to 1220~1260°C, keep it warm for 2h~2.5h, and austenitize the composition;
[0049] 2) Rolling in the recrystallization zone: the starting temperature of rolling in the recrystallization zone is 1150°C, rolling 3 passes, and the final rolling temperature in the recrystallization zone is controlled at 1030~1050°C to obtain an intermediate billet, which is then rolled in the recrystallization zone The reduction rate of each pass is controlled at 25%~40%.
[0050] 3) Rolling in the non-recrystallized area: when the intermediate billet i...
Embodiment 3
[0056] The specific composition of the slab in this embodiment is by weight percentage: C: 0.09%, Si: 0.03%, Mn: 1.80%, Mo: 0.15%, Nb: 0.050%, Ti: 0.19%, Al: 0.025%, B: 0.002%, P: 0.006%, S: 0.006%, Ca: 0.005%, the rest is Fe and unavoidable impurities, of which the carbon equivalent Ceq=0.42, which ensures excellent weldability.
[0057] The specific production process is carried out according to the following steps:
[0058] 1) Billet heating: heat the billet to 1220~1260°C, keep it warm for 2h~2.5h, and austenitize the composition;
[0059] 2) Rolling in the recrystallization zone: the starting temperature of rolling in the recrystallization zone is 1150°C, rolling 3 passes, and the final rolling temperature in the recrystallization zone is controlled at 1030~1050°C to obtain an intermediate billet, which is then rolled in the recrystallization zone The reduction rate of each pass is controlled at 25%~40%.
[0060] 3) Rolling in the non-recrystallized area: when the inter...
PUM
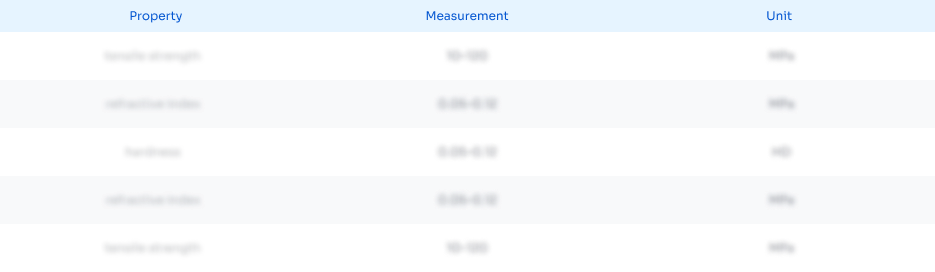
Abstract
Description
Claims
Application Information

- Generate Ideas
- Intellectual Property
- Life Sciences
- Materials
- Tech Scout
- Unparalleled Data Quality
- Higher Quality Content
- 60% Fewer Hallucinations
Browse by: Latest US Patents, China's latest patents, Technical Efficacy Thesaurus, Application Domain, Technology Topic, Popular Technical Reports.
© 2025 PatSnap. All rights reserved.Legal|Privacy policy|Modern Slavery Act Transparency Statement|Sitemap|About US| Contact US: help@patsnap.com