Method for continuous production of polyformaldehyde dimethyl ether
A technology of polyoxymethylene dimethyl ether and paraformaldehyde, which is applied in chemical instruments and methods, preparation of organic compounds, organic chemistry, etc., can solve the problems of environmental pollution, corrosion of liquid acid catalysts, and high production costs
- Summary
- Abstract
- Description
- Claims
- Application Information
AI Technical Summary
Problems solved by technology
Method used
Image
Examples
Embodiment 1
[0030] Add 30 ml of Nafion resin with a particle size of 0.5 to 1.0 mm in a reaction tube with an inner diameter of 2.5 mm. The reaction temperature is controlled at 140 °C, the reaction pressure is 3 MPa, and the liquid volume hourly space velocity (LHSV) is 1 hr. -1 , the mass ratio of methylal and paraformaldehyde is 2.0, the reaction product is sampled after cooling, and analyzed by gas chromatography, wherein DMM 32.2%, MeOH 4.0%, DMM 2 20.6%, DMM 3-8 27.0 %, DMM n (n>8) not detected.
Embodiment 2
[0032] Add 30 ml of Nafion resin with a particle size of 0.5 to 1.0 mm in a reaction tube with an inner diameter of 2.5 mm. The reaction temperature is controlled at 160 °C, the reaction pressure is 3 MPa, and the liquid volume hourly space velocity (LHSV) is 1 hr. -1 , the mass ratio of methylal and paraformaldehyde is 2.0, the reaction product is sampled after cooling, and analyzed by gas chromatography, wherein DMM 30.6%, MeOH 3.9%, DMM 2 20.2%, DMM 3-8 26.7 %, DMM n (n>8) not detected.
Embodiment 3
[0034] Add 30 ml of Nafion resin with a particle size of 0.5 to 1.0 mm in a reaction tube with an inner diameter of 2.5 mm. The reaction temperature is controlled at 140 °C, the reaction pressure is 3 MPa, and the liquid volume hourly space velocity (LHSV) is 0.5 hr. -1 , the mass ratio of methylal and paraformaldehyde is 2.0, the reaction product is sampled after cooling, and analyzed by gas chromatography, wherein DMM 26.2%, MeOH 4.0%, DMM 2 18.4 %, DMM 3-8 30.0 %, DMM n (n>8) not detected.
PUM
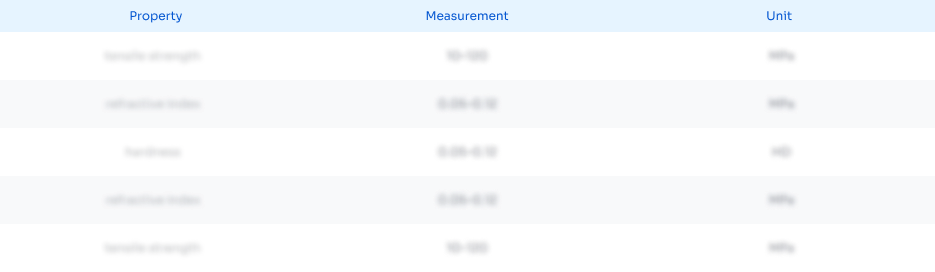
Abstract
Description
Claims
Application Information

- R&D
- Intellectual Property
- Life Sciences
- Materials
- Tech Scout
- Unparalleled Data Quality
- Higher Quality Content
- 60% Fewer Hallucinations
Browse by: Latest US Patents, China's latest patents, Technical Efficacy Thesaurus, Application Domain, Technology Topic, Popular Technical Reports.
© 2025 PatSnap. All rights reserved.Legal|Privacy policy|Modern Slavery Act Transparency Statement|Sitemap|About US| Contact US: help@patsnap.com