Li2MnO3 and LiCoO2 composite anode material
A technology of composite cathode materials and composite oxides, applied in battery electrodes, electrical components, circuits, etc., can solve the problems of complicated operation, environmental protection and energy saving, etc., achieve good repeatability, improve electrochemical performance, save energy The effect of production costs
- Summary
- Abstract
- Description
- Claims
- Application Information
AI Technical Summary
Problems solved by technology
Method used
Image
Examples
Embodiment 1
[0030] Example 1: 0.075Li 2 MnO 3 0.925LiCoO 2 Composite cathode material
[0031] Using lithium acetate, manganese acetate, cobalt acetate and sodium hydroxide as starting materials, ball mill 1.5mmol manganese acetate, 18.5mmol cobalt acetate and 25.8mmol lithium acetate at room temperature for 0.5h, then add 137.4mmol sodium hydroxide at room temperature Ball milled for 2.5 hours to obtain a mixture, the molar ratio of sodium hydroxide to total metal ions was 3:1. The mixture was dried at 180°C for 3 h, then ground into powder and loaded into a crucible. Heat in a box furnace at a rate of 4°C / min to 350°C for 3 hours, then raise the temperature to 900°C and heat for 10 hours, then cool to room temperature with the furnace. After washing several times with deionized water, filter, dry the filter residue at 180°C for 3 hours, transfer the sample to a crucible after drying, heat treatment in a box furnace at 900°C for 6 hours, and anneal at room temperature to obtain 0.075...
Embodiment 2
[0032] Example 2: 0.025Li 2 MnO 3 0.975LiCoO 2 Composite cathode material
[0033] Using lithium acetate, manganese acetate, cobalt acetate and sodium hydroxide as starting materials, ball mill 0.5mmol manganese acetate, 19.5mmol cobalt acetate and 24.6mmol lithium acetate at room temperature for 0.5h, then add 133.8mmol sodium hydroxide at room temperature Ball milled for 2.5 hours to obtain a mixture, the molar ratio of sodium hydroxide to total metal ions was 3:1. The mixture was dried at 180°C for 3 h, then ground into powder and loaded into a crucible. Heat in a box furnace at a rate of 4°C / min to 350°C for 3 hours, then raise the temperature to 900°C and heat for 10 hours, then cool to room temperature with the furnace. After washing several times with deionized water, filter, dry the filter residue at 180°C for 3 hours, transfer the sample to a crucible after drying, heat treatment in a box furnace at 900°C for 6 hours, and anneal at room temperature to obtain 0.025...
Embodiment 3
[0034] Example 3: 0.05Li 2 MnO 3 0.95LiCoO 2 Composite cathode material
[0035] Using lithium acetate, manganese acetate, cobalt acetate and sodium hydroxide as raw materials, 1mmol of manganese acetate, 19mmol of cobalt acetate and 25.2mmol of lithium acetate were ball-milled at room temperature for 0.5h, and then 135.6mmol of sodium hydroxide was added and ball-milled for 2.5h at room temperature. A mixed material was obtained, and the molar ratio of sodium hydroxide to total metal ions was 3:1. The mixture was dried at 180°C for 3 h, then ground into powder and loaded into a crucible. Heat in a box furnace at a rate of 4°C / min to 350°C for 3 hours, then raise the temperature to 900°C and heat for 10 hours, then cool to room temperature with the furnace. After washing several times with deionized water, filter, dry the filter residue at 180°C for 3 hours, transfer the sample to a crucible after drying, heat treatment in a box furnace at 900°C for 6 hours, and anneal at ...
PUM
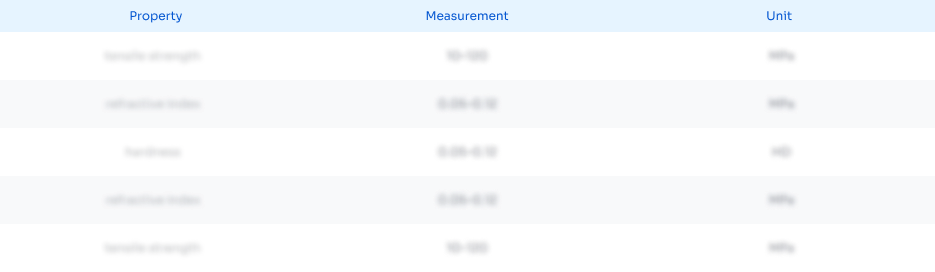
Abstract
Description
Claims
Application Information

- Generate Ideas
- Intellectual Property
- Life Sciences
- Materials
- Tech Scout
- Unparalleled Data Quality
- Higher Quality Content
- 60% Fewer Hallucinations
Browse by: Latest US Patents, China's latest patents, Technical Efficacy Thesaurus, Application Domain, Technology Topic, Popular Technical Reports.
© 2025 PatSnap. All rights reserved.Legal|Privacy policy|Modern Slavery Act Transparency Statement|Sitemap|About US| Contact US: help@patsnap.com