Method for controlling steel slab gap in heating furnace
A heating furnace and gap technology, applied in the direction of heat treatment furnace, heat treatment process control, furnace, etc., can solve the problems of non-dynamic adjustment, inability to dynamically adjust the loading stroke, increase the difficulty of heating control of wide and thick slabs, etc., to reduce stickiness The frequency of uneven heating of steel and slabs, the effect of reducing quality defects and improving production efficiency
- Summary
- Abstract
- Description
- Claims
- Application Information
AI Technical Summary
Problems solved by technology
Method used
Image
Examples
Embodiment
[0063] The invention relates to a method for controlling the billet gap in a heating furnace. The method comprises the control of the steel loading stroke, the control of the steel loading vacancy and the position tracking of the furnace map. The action flow of steel loading is as follows: the steel loading machine is responsible for sending steel billets of different specifications into the heating furnace for heating. First, the arm of the loading machine pushes the slab to be positioned in front of the furnace, then backs up, lifts up the slab, advances it to the target position, and returns to the original position after falling, that is, a steel loading task is completed. The calculated value of the loaded steel stroke is determined by installing an incremental pulse encoder at the end of the shaft of the variable frequency motor, and then connecting it to the counting module of the on-site signal acquisition station through a shielded cable to complete signal processing. ...
PUM
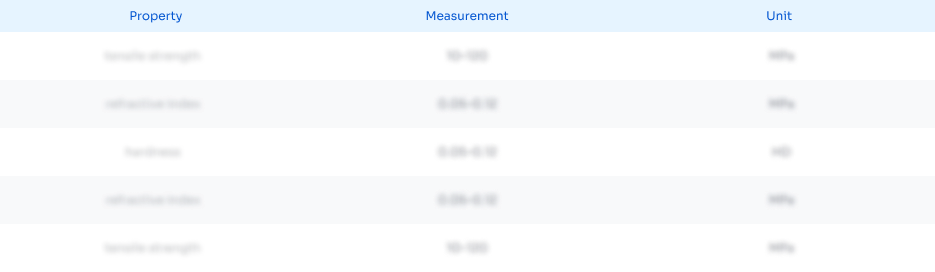
Abstract
Description
Claims
Application Information

- R&D
- Intellectual Property
- Life Sciences
- Materials
- Tech Scout
- Unparalleled Data Quality
- Higher Quality Content
- 60% Fewer Hallucinations
Browse by: Latest US Patents, China's latest patents, Technical Efficacy Thesaurus, Application Domain, Technology Topic, Popular Technical Reports.
© 2025 PatSnap. All rights reserved.Legal|Privacy policy|Modern Slavery Act Transparency Statement|Sitemap|About US| Contact US: help@patsnap.com