Anti-crack expanding agent and preparation method thereof
A technology of expansion agent and weight ratio, which is applied in the field of concrete additives, can solve the problems of decreased bonding strength, inapplicability in places with special requirements for strength and anti-seepage, and insignificant compensation for plastic shrinkage, so as to improve waterproof and anti-seepage. The effect of improving permeability and improving compactness
- Summary
- Abstract
- Description
- Claims
- Application Information
AI Technical Summary
Problems solved by technology
Method used
Image
Examples
Embodiment 1
[0034] Embodiment 1, in the present embodiment, the anti-crack expansion agent adopts the mass ratio of calcium oxide clinker 37%, gypsum 18%, dickite 34%, fly ash 7%, wollastonite powder 4% ratio, calcium oxide clinker , Gypsum, and dickite are ground to a certain fineness in a mill, and then mixed with fly ash and wollastonite powder. Or add 37% of calcium oxide clinker, 18% of gypsum, 34% of dickite, 7% of fly ash, and 4% of wollastonite powder into the mill for uniform grinding, and transport them to the homogenization warehouse for homogenization . Then the anti-crack expansion agent is obtained.
[0035] The calcium oxide clinker in this embodiment is a single substance obtained by calcining limestone powder above 1500°C, and its weight ratio and its components are as follows: SiO 2 6.95%, Al 2 o 3 5.50%; Fe 2 o 3 2.21%, CaO 82.04%, MgO 0.82%, loss on ignition 1.26%, and the balance is unavoidable impurities, and the weight percentage of free calcium oxide in th...
Embodiment 2
[0056] Embodiment 2, in the present embodiment, the anti-crack expansion agent adopts the mass ratio of calcium oxide clinker 39%, gypsum 19%, dickite 33%, fly ash 6%, wollastonite powder 3% ratio, calcium oxide clinker , Gypsum, and dickite are ground to a certain fineness in a mill, and then mixed with fly ash and wollastonite powder. Or add 39% of calcium oxide clinker, 19% of gypsum, 33% of dickite, 6% of fly ash, and 3% of wollastonite powder into the mill for uniform grinding, and transport it to the homogenization warehouse for homogenization . Then the anti-crack expansion agent is obtained. Other can refer to embodiment 1.
Embodiment 3
[0057] Embodiment 3, in the present embodiment, the anti-crack expansion agent adopts a mass ratio of calcium oxide clinker 36%, gypsum 20%, dickite 34%, fly ash 8%, wollastonite powder 2%, and calcium oxide clinker , Gypsum, and dickite are ground to a certain fineness in a mill, and then mixed with fly ash and wollastonite powder. Or add 36% of calcium oxide clinker, 20% of gypsum, 34% of dickite, 8% of fly ash, and 2% of wollastonite powder into the mill for uniform grinding, and transport them to the homogenization warehouse for homogenization . Then the anti-crack expansion agent is obtained. Other can refer to embodiment 1.
PUM
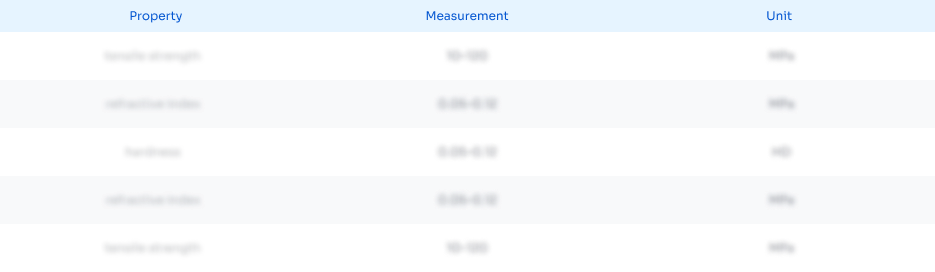
Abstract
Description
Claims
Application Information

- R&D
- Intellectual Property
- Life Sciences
- Materials
- Tech Scout
- Unparalleled Data Quality
- Higher Quality Content
- 60% Fewer Hallucinations
Browse by: Latest US Patents, China's latest patents, Technical Efficacy Thesaurus, Application Domain, Technology Topic, Popular Technical Reports.
© 2025 PatSnap. All rights reserved.Legal|Privacy policy|Modern Slavery Act Transparency Statement|Sitemap|About US| Contact US: help@patsnap.com