Bacillus subtilis RB and application thereof
A technology of Bacillus subtilis and enzyme bacteria, applied in the application field of Bacillus subtilis RB, can solve the problems of low utilization rate of cellulose, hemicellulose and protein, poor adaptability of enzymes, inability to synthesize amino acids, etc., and achieve adaptability The effect of strong, increased output and strong processing capacity
- Summary
- Abstract
- Description
- Claims
- Application Information
AI Technical Summary
Problems solved by technology
Method used
Image
Examples
Embodiment 1
[0016] Embodiment 1, bacillus subtilis ( Bacillus subtilis ) separation of RB
[0017] Mix 10g of beneficial microorganisms isolated and screened from nature evenly with the nutrient base, which contains 5-10g of cornstarch, 5-10g of brown sugar and 10-20g of wheat bran, pH 6.0-7.0, humidity 30-35%, and then Add 0.005-0.05 g of hydroxylamine or ethyl imine; at a temperature of 25-35° C. with a temperature difference of 8-10° C., cultivate for 2-3 days, and use an inoculation loop to screen out Bacillus subtilis RB. The nutrient base may also include 3-5 g of fish meal, 3-5 g of vegetable cake or 35-50 g of polished rice bran.
Embodiment 2
[0018] Embodiment 2, the cultivation of Bacillus subtilis RB
[0019] Bacillus subtilis RB medium: sucrose 50g, (NH 4 ) 2 SO 4 6g, K 2 SO 4 2.5g, CaSO 4 2.5g, agar powder 15g and distilled water 1000mL.
[0020] The culture conditions are as follows: the temperature is 30° C., and the pH is 6.0.
Embodiment 3
[0021] Embodiment 3, the application of Bacillus subtilis RB
[0022] The enzyme bacteria of the present invention is obtained by mixing Bacillus subtilis RB with commercially available enzyme bacteria in a weight ratio of 1-2:5, that is, the mass percentage of Bacillus subtilis RB in the enzyme bacteria is 20%-40%.
[0023] Mix and stir 1kg of enzyme bacteria with 100kg of sludge, 100kg of poultry manure or 100kg of crop straw, and carry out open aerobic solid-state fermentation at a temperature of 60°C for 7 days, and then enter the process of drying, crushing, and manufacturing through a conveying system. Grain and sieve to obtain amino acid fertilizer. Exhaust gases from the drying step can be pumped into a tank and returned to the fermentation step.
[0024] 1 kg of ferment bacteria was mixed with 100 kg of sludge, 100 kg of poultry manure or 100 kg of crop stalks, and fermented in the same way as above. As a control test, the results are shown in Table 1.
[0025] Th...
PUM
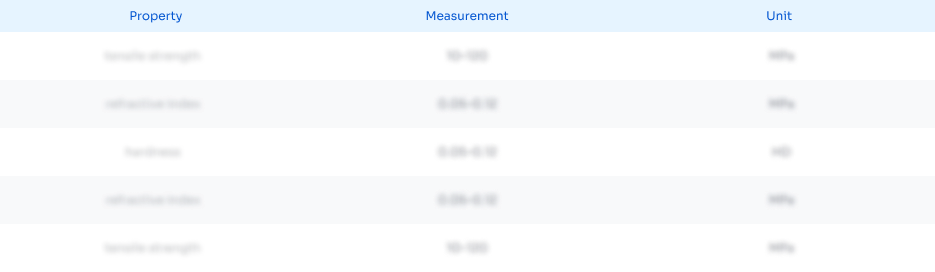
Abstract
Description
Claims
Application Information

- Generate Ideas
- Intellectual Property
- Life Sciences
- Materials
- Tech Scout
- Unparalleled Data Quality
- Higher Quality Content
- 60% Fewer Hallucinations
Browse by: Latest US Patents, China's latest patents, Technical Efficacy Thesaurus, Application Domain, Technology Topic, Popular Technical Reports.
© 2025 PatSnap. All rights reserved.Legal|Privacy policy|Modern Slavery Act Transparency Statement|Sitemap|About US| Contact US: help@patsnap.com