Organic and inorganic composite flushing liquid as well as preparation method and applications thereof
An inorganic composite and flushing fluid technology, which is applied in the field of oil well cement cementing, can solve the problems of poor temperature resistance, low flushing efficiency, and high cementing pump pressure, and achieves high cementing strength, good flushing effect, and high flushing efficiency. Effect
- Summary
- Abstract
- Description
- Claims
- Application Information
AI Technical Summary
Problems solved by technology
Method used
Image
Examples
preparation example Construction
[0025] The preparation method of the above-mentioned organic-inorganic composite rinsing solution comprises the following steps: according to the above-mentioned mass ratio, firstly add sodium pyrophosphate into clear water and stir evenly to fully dissolve it, then add sodium silicate and stir for 10-20 minutes, heat up to 50°C, Add polysorbate-80, alkylphenol polyoxyethylene ether and sodium dodecylbenzenesulfonate respectively and stir for 30-40 minutes.
[0026] Use of the above-mentioned organic-inorganic composite flushing fluid in flushing oil-based mud and water-based mud.
Embodiment 1
[0029] Take 30g of clear water, add 7g of sodium pyrophosphate and stir evenly to fully dissolve it, then add 15g of sodium silicate and stir for 10 minutes, then add 25g of polysorbate-80, 15g of octylphenol polyoxyethylene ether, 8 g of sodium dodecylbenzene sulfonate was stirred for 30-40 minutes to obtain organic-inorganic composite rinse solution sample 1.
Embodiment 2
[0031] Take 26g of clear water, add 10g of sodium pyrophosphate and stir evenly to fully dissolve it, then add 20g of sodium silicate and stir for 15 minutes, then add 20g of polysorbate-80, 14g of octylphenol polyoxyethylene ether, 10 g of sodium dodecylbenzene sulfonate was stirred for 30-40 minutes to obtain organic-inorganic composite flushing solution sample 2.
PUM
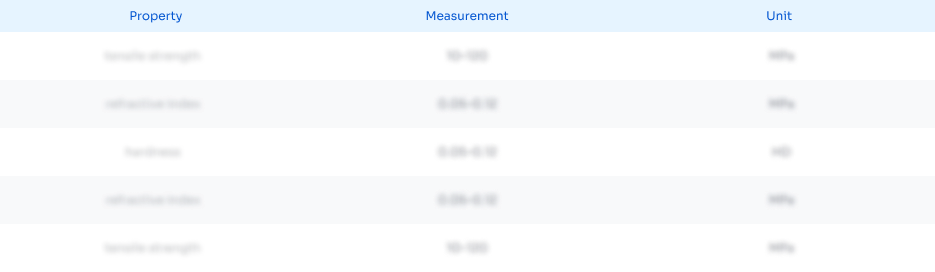
Abstract
Description
Claims
Application Information

- R&D
- Intellectual Property
- Life Sciences
- Materials
- Tech Scout
- Unparalleled Data Quality
- Higher Quality Content
- 60% Fewer Hallucinations
Browse by: Latest US Patents, China's latest patents, Technical Efficacy Thesaurus, Application Domain, Technology Topic, Popular Technical Reports.
© 2025 PatSnap. All rights reserved.Legal|Privacy policy|Modern Slavery Act Transparency Statement|Sitemap|About US| Contact US: help@patsnap.com