Process for cleaning damage layer of reactive ion etching (RIE) flocking surface of crystalline silicon
A surface damage and crystalline silicon technology, which is applied in the cleaning process of the surface damage layer of crystalline silicon RIE texturing, can solve the problems affecting the light trapping effect on the surface of silicon wafers, and achieve the effects of saving raw materials, simple process, and reduced process flow
- Summary
- Abstract
- Description
- Claims
- Application Information
AI Technical Summary
Problems solved by technology
Method used
Examples
Embodiment 1
[0017] A kind of cleaning process of crystalline silicon RIE cashmere surface damage layer, comprises the following steps:
[0018] (1) Pre-clean the surface of the damaged layer of the silicon wafer after RIE etching with deionized water;
[0019] (2) Prepare cleaning solution, the cleaning solution is HF, HCl and H 2 o 2 A mixed solution of , and HF, HCl and H 2 o 2 The volume ratio is 3:3:1;
[0020] (3) Use the cleaning solution prepared in step (2) to clean the silicon wafer for 15 minutes to remove the damaged layer on the surface after RIE etching, and reduce the recombination rate of photogenerated carriers;
[0021] (4) Clean the silicon wafer with deionized water and dry it for later use.
[0022] The minority carrier lifetime of the silicon wafer after cleaning in this embodiment is 4.53 μs
Embodiment 2
[0024] A kind of cleaning process of crystalline silicon RIE cashmere surface damage layer, comprises the following steps:
[0025] (1) Pre-clean the surface of the damaged layer of the silicon wafer after RIE etching with deionized water;
[0026] (2) Prepare cleaning solution, the cleaning solution is HF, HCl and H 2 o 2 A mixed solution of , and HF, HCl and H 2 o 2 The volume ratio is 3:7:2;
[0027] (3) Use the cleaning solution prepared in step (2) to clean the silicon wafer to remove the damaged layer for 6 minutes, remove the damaged layer on the surface after RIE etching, and reduce the recombination rate of photogenerated carriers;
[0028] (4) Clean the silicon wafer with deionized water and dry it for later use.
[0029] The minority carrier lifetime of the silicon wafer after cleaning in this embodiment is 8.2 μs.
Embodiment 3
[0031] A kind of cleaning process of crystalline silicon RIE cashmere surface damage layer, comprises the following steps:
[0032] (1) Pre-clean the surface of the damaged layer of the silicon wafer after RIE etching with deionized water;
[0033] (2) Prepare cleaning solution, the cleaning solution is HF, HCl and H 2 o 2 A mixed solution of , and HF, HCl and H 2 o 2 The volume ratio is 15:15:1;
[0034] (3) Use the cleaning solution prepared in step (2) to clean the silicon wafer to remove the damaged layer for 4 minutes, remove the damaged layer on the surface after RIE etching, and reduce the recombination rate of photogenerated carriers;
[0035] (4) Clean the silicon wafer with deionized water and dry it for later use.
[0036] The minority carrier lifetime of the silicon wafer after cleaning in this embodiment is 5.97 μs.
[0037] This cleaning process basically has no effect on the reflectivity of the silicon wafer, and the minority carrier lifetime of the silico...
PUM
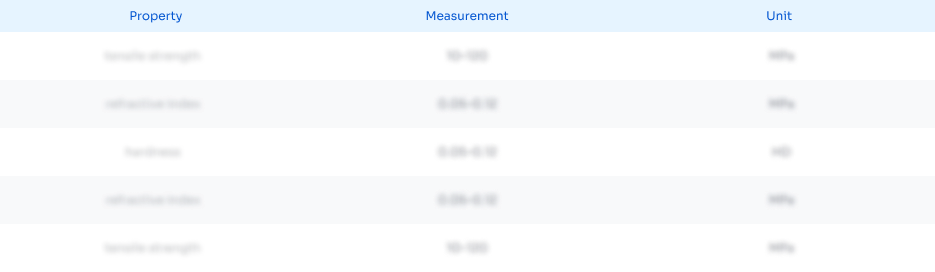
Abstract
Description
Claims
Application Information

- R&D
- Intellectual Property
- Life Sciences
- Materials
- Tech Scout
- Unparalleled Data Quality
- Higher Quality Content
- 60% Fewer Hallucinations
Browse by: Latest US Patents, China's latest patents, Technical Efficacy Thesaurus, Application Domain, Technology Topic, Popular Technical Reports.
© 2025 PatSnap. All rights reserved.Legal|Privacy policy|Modern Slavery Act Transparency Statement|Sitemap|About US| Contact US: help@patsnap.com